1. **Pad Overlap**
1. The overlap of PCB pads (excluding surface pads) refers to the overlap of the holes, which can lead to drill breakage and hole damage due to multiple drilling at a single location during the drilling process.
2. In multi-layer PCBs, when two holes overlap, one may correspond to an isolation layer while the other connects to a different layer (such as a ground plane). Consequently, when the backsheet is stretched, it can create a separator, resulting in scrap.
2. **Misuse of the Graphics Layer**
1. Some graphics layers contain unnecessary connections. For instance, a design intended for a four-layer board may mistakenly include over five layers of circuits, leading to confusion.
2. PCB design should minimize complications. Using Protel software as an example, all lines on each layer should be drawn and labeled accordingly. This ensures that during data processing, if a board layer is not selected, circuits may be inadvertently cut, or a short circuit may occur if a marked line on the board layer is incorrectly chosen. Thus, maintaining the integrity and clarity of the graphics layer is crucial throughout the design process.
3. This practice contradicts traditional design norms. For example, placing component surfaces on the bottom layer while designing the soldering surfaces on the top layer creates challenges.
3. **Random Placement of Text**
1. The placement of text on the pad can complicate the on-off testing of printed circuit boards and the soldering of components.
2. If the text is designed too small, screen printing becomes difficult; if too large, the characters may overlap and become indistinguishable.
4. **Setting of Single Pad Aperture**
1. Typically, single-sided pads are not drilled. If drilling is necessary, the hole diameter should be set to zero. If a specific value is assigned, drilling data will generate coordinates for that position, leading to potential issues.
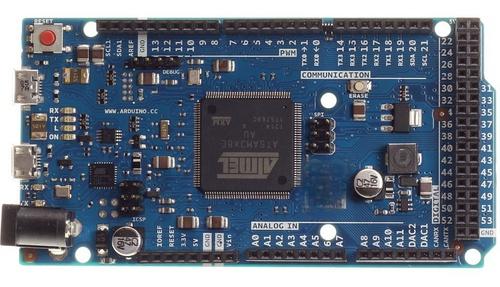
2. Single-sided pads should be distinctly marked if they are drilled.
5. Artboard with filled blocks
The drawing board containing filler blocks can pass inspection in the Democratic Republic of Congo during circuit design; however, it is unsuitable for processing. Consequently, solder mask data cannot be generated directly for such pads. When applying solder resist, the filler block area will be obscured, complicating the soldering of the device.
6. Formation of electricity involves the flower cushion and connection
Due to the flower cushion pattern in power supply design, the ground layer is reversed compared to the actual printed board, and all connection lines are isolated, which should be clear to the designer. It is important to exercise caution when drawing isolation lines for power supply groups or grounding types. No gaps should be present that could short-circuit two power supply sets or block the connection area (to separate one power supply set).
7. The definition of processing levels is unclear
1. The single board is designed on the top layer. Without descriptions on both front and back, the manufactured panel may be fitted with devices instead of soldered.
2. For instance, when designing a four-layer board, use the top layer (1), middle layers (2), and bottom layer (4), but if they are not processed in this order, clarification is required.
8. Excessive or inadequately sized filling blocks in the design
1. There is data loss in the lighting drawing, rendering it incomplete.
2. As filling blocks are drawn line by line in the light drawing data processing, the volume of light drawing data generated is substantial, complicating data processing.
9. Surface mount device pads are too short
This is relevant for switch testing. For densely arranged surface mount devices, the distance between two legs is minimal, and pads are very thin. To install test pins, a staggered arrangement (up and down or left and right) is necessary. If pad design is overly short, it may not impact device installation but could hinder proper opening of test pins.
10. Large area grid spacing is insufficient
The edges between lines forming large-area grid lines are too narrow (less than 0.3 mm). During the manufacturing of printed circuit boards, damaged films often adhere to the circuit board post-image display, leading to wire breakage.
11. Large copper foil area is too close to the outer frame
The distance between large copper foil areas and the outer frame should be at least 0.2 mm. When milling shapes, such as copper foil, this proximity may cause the foil to warp and the solder mask to detach.
12. Outline frame design lacks clarity
Some customers have created contour lines on reserved, board, and top layers, but inconsistencies in these contour lines hinder printed circuit board manufacturers from determining which line should take precedence.
13. Graphic design lacks uniformity
Uneven plating during pattern plating can adversely affect quality.
14. Abnormal hole length is insufficient
The length-to-width ratio of special-shaped holes should be ≥2:1, with a width greater than 1.0 mm. Otherwise, the drilling machine may break while processing these holes, complicating the process and increasing costs.