—
**Causes of Failure of Blind Via Interconnection in HDI Boards**
1. Excessive Energy During Laser Ablation: Laser ablation is the predominant method for creating blind vias. While CO2 lasers cannot directly ablate copper layers, specially treating the copper surface to enhance its absorption of infrared wavelengths can cause the copper to rapidly reach very high temperatures. Typically, the inner copper at the base of the blind via becomes browned, as browned copper reflects less laser light and has a rough surface that increases diffuse reflection, thereby enhancing light absorption. Additionally, the browned copper surface has an organic layer structure that further promotes light absorption. Consequently, if the laser energy is excessive during drilling, it may recrystallize the inner copper layer at the base of the blind via, leading to alterations in the copper’s structural integrity.
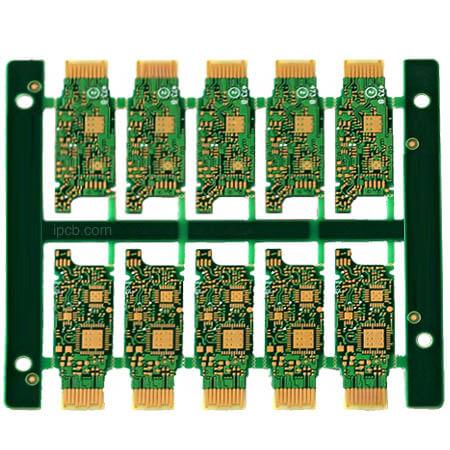
2. **Desmear is not clean**
The removal of epoxy drilling or slag before blind hole electroplating is a crucial process that significantly affects the reliability of the connection between the copper of the hole wall and the inner layer of copper. A thin resin layer can render the blind hole semi-conductive. During the E-TEST test, this may pass due to the stylus pressure, but issues such as open circuits or contact failures can arise after the board is assembled. For instance, in mobile phone boards with around 70,000 to 100,000 blind holes, occasional errors in glue removal are inevitable. As the cavitation potion systems of various manufacturers have been refined, closely monitoring the bath liquid and promptly replacing it before problems arise is essential for maintaining the desired yield.
3. **The quality of the copper plating layer on the surface of the inner connecting pad is abnormal**
Abnormal quality of the copper-plated layer on the surface of the inner connecting pad can also lead to blind hole ICD issues. The physical properties of the copper-plated layer—such as ductility, tensile strength, internal stress, and compactness—are crucial for the reliability of the blind hole. These properties depend on the structure and chemical composition of the copper layer. The image shows ICD caused by rough plating on the inner layer’s surface at the bottom of the blind hole. Such rough surfaces can lead to poor glue removal and crystallization issues with the copper surface itself, resulting in defects like poor bonding between electroless copper and inner layer copper. Consequently, ICDs are more likely when subjected to significant stress.
4. **The difference in material expansion and contraction is too large**
Material matching also greatly affects the interconnection reliability of blind vias. Figures 8 and 9 illustrate ICD in the secondary build-up board plating blind hole filling. The secondary build-up board uses RCC material for L1-L2 and LDP material for the L2-L3 plating blind hole filling layer. The high temperature of lead-free soldering causes these materials, with significant differences in their Coefficient of Thermal Expansion (CTE), to expand and contract differently. This discrepancy increases the probability of blind hole ICD in the LDP layer. Thus, careful selection and matching of materials are crucial when producing multi-layer laminates.
5. **Halogen-free RCC increases the probability of blind hole ICD**
Halogen-free RCC material, developed to meet RoHS requirements, does not contain halogens and has excellent flame resistance. Its primary modification involves using phosphorus (P) and nitrogen (N) to replace halogens, reducing the polarity of the polymer chain and increasing the resin’s molecular weight. The addition of fillers like aluminum oxide further alters the material’s characteristics, making halogen-free RCC different from conventional epoxy resins. This can lead to issues when used with existing electroplating solutions, potentially causing thin plating and increased ICD occurrences.
6. **Excessive manual soldering heat or too many reworks**
In HDI boards, manual soldering is sometimes required for certain parts during assembly. The quality of manual soldering is greatly affected by the temperature used, the skill of the soldering personnel, and the number of reworks performed. Excessive heat or frequent reworks can significantly impact soldering quality.