With the ongoing advancement of science and technology, PCBA has gradually become familiar to many. It serves as a crucial electronic component, supporting various electronic elements and providing essential circuit connections. Its presence is widespread in today’s urban environments. What else might you not know about its functions? Let’s delve into “PCBA selection criteria and associated anti-static methods.
[Key Points of PCBA Selection]
PCBA is the heart of electronic products, much like the pivotal role of the Chinese army in a three-army battle. The reliability, usability, and stability of a product are closely tied to the quality of its PCBA. Therefore, when purchasing PCBA, it is imperative to focus on quality control points and to assess each PCBA board with a discerning eye to ensure it meets the application requirements of electronic devices.
1. The reliability of PCBA component soldering
The reliability of soldering on PCB circuit boards and their components directly impacts the performance of electronic products during operation. As products are used over time, circuit boards may experience oxidation, thermal stress, drops, and excessive loads, which can lead to issues even in boards that initially passed quality checks. Consequently, these factors can result in welding problems and product failures.

In addition, the choice between brand original components and alternatives is crucial for the quality of electronic products in PCBA processing. Many second-hand or counterfeit components may fail dramatically after prolonged use. The same applies to PCB circuit boards. Depending on the product’s application environment, it’s essential to consider factors that prevent PCB deformation and heat-related issues when purchasing PCBA, along with rigorous testing protocols.
2. PCBA Aging Test Performance Report
For large volume production, stringent aging tests are imperative. These tests assess the stability and reliability of the PCBA under extremely harsh usage conditions. To cut costs, many companies skip this vital step, leading to defective products reaching customers and resulting in significant losses. Therefore, it is advisable to request aging test requirements for bulk orders, establish aging test fixtures, and insist that suppliers provide performance reports for aging tests.
3. PCBA Assembly Process Management
The management of the assembly process for PCBA boards, enclosures, and packaging is equally important. Improper handling during assembly can damage components on otherwise functioning PCBA boards, resulting in defects post-assembly. PCBA suppliers should implement strict operational guidelines and ensure workers adhere to these procedures.
4. Cleanliness of PCBA Board Surface
The cleanliness of the PCBA board’s surface is critical. Residual solder, flux, and other contaminants can pose unpredictable risks in the future use of electronic products. Therefore, it is essential for PCBA manufacturers to perform professional ultrasonic cleaning on all batches of PCBA panels and to avoid finger contamination of the panels.
5. Evaluating After-Sales Service Capabilities of PCBA Suppliers
Assessing a supplier’s after-sales service capabilities is vital when purchasing PCBA. Even the most experienced professionals can make mistakes. As mass production continues to expand, unexpected issues are bound to arise. In such cases, the ability of PCBA manufacturers to respond swiftly and collaborate effectively is crucial.
6. Allowing Manufacturers Adequate Profit When Purchasing PCBA
With the rapid advancement of the circuit board and PCBA processing industries, PCBA pricing has become very transparent. A little research or comparison can help avoid being overcharged. Profit drives a company’s ability to serve customers; without profit, service quality and control diminish. Therefore, while purchasing PCBA, it’s essential to move beyond the mindset of relentless price bargaining and provide reasonable profits to PCBA manufacturers, benefiting the overall quality of your products and your own interests.
[Anti-Static Precautions During PCBA Processing]
When processing PCBA, personnel must meticulously follow the bill of materials, PCB silkscreen, and outsourcing requirements when inserting or mounting components. However, electronic components often generate static electricity, which, if not managed, can lead to electromagnetic pulses during discharge, causing computation errors and potentially damaging devices and circuits. Implementing anti-static measures is crucial to protect both machines and components. Here are some strategies to prevent static electricity:
1. All personnel handling components and products should wear anti-static clothing, bracelets, and shoes.
2. The anti-static system must include a reliable grounding device, with the anti-static ground wire kept separate from the power neutral wire and lightning protection ground.
3. Treat all components as electrostatic sensitive devices.
4. Use anti-static work surfaces and containers for components and semi-finished products during operations.
5. Ensure welding equipment is properly grounded, and electric soldering irons are anti-static types that must be tested before use.
6. Warehouse personnel should wear anti-static gloves during material handling and IQC testing, using grounded meters and covering work surfaces with anti-static rubber pads.
7. Regularly inspect all anti-static tools, setups, and materials to ensure they meet required conditions.
If you have any PCB manufacturing needs, please do not hesitate to contact me.Contact me
[Key Points of PCBA Selection]
PCBA is the heart of electronic products, much like the pivotal role of the Chinese army in a three-army battle. The reliability, usability, and stability of a product are closely tied to the quality of its PCBA. Therefore, when purchasing PCBA, it is imperative to focus on quality control points and to assess each PCBA board with a discerning eye to ensure it meets the application requirements of electronic devices.
1. The reliability of PCBA component soldering
The reliability of soldering on PCB circuit boards and their components directly impacts the performance of electronic products during operation. As products are used over time, circuit boards may experience oxidation, thermal stress, drops, and excessive loads, which can lead to issues even in boards that initially passed quality checks. Consequently, these factors can result in welding problems and product failures.
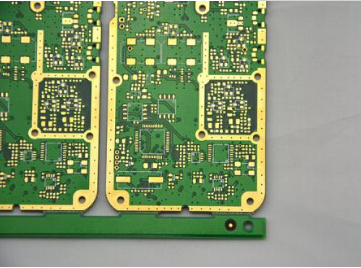
In addition, the choice between brand original components and alternatives is crucial for the quality of electronic products in PCBA processing. Many second-hand or counterfeit components may fail dramatically after prolonged use. The same applies to PCB circuit boards. Depending on the product’s application environment, it’s essential to consider factors that prevent PCB deformation and heat-related issues when purchasing PCBA, along with rigorous testing protocols.
2. PCBA Aging Test Performance Report
For large volume production, stringent aging tests are imperative. These tests assess the stability and reliability of the PCBA under extremely harsh usage conditions. To cut costs, many companies skip this vital step, leading to defective products reaching customers and resulting in significant losses. Therefore, it is advisable to request aging test requirements for bulk orders, establish aging test fixtures, and insist that suppliers provide performance reports for aging tests.
3. PCBA Assembly Process Management
The management of the assembly process for PCBA boards, enclosures, and packaging is equally important. Improper handling during assembly can damage components on otherwise functioning PCBA boards, resulting in defects post-assembly. PCBA suppliers should implement strict operational guidelines and ensure workers adhere to these procedures.
4. Cleanliness of PCBA Board Surface
The cleanliness of the PCBA board’s surface is critical. Residual solder, flux, and other contaminants can pose unpredictable risks in the future use of electronic products. Therefore, it is essential for PCBA manufacturers to perform professional ultrasonic cleaning on all batches of PCBA panels and to avoid finger contamination of the panels.
5. Evaluating After-Sales Service Capabilities of PCBA Suppliers
Assessing a supplier’s after-sales service capabilities is vital when purchasing PCBA. Even the most experienced professionals can make mistakes. As mass production continues to expand, unexpected issues are bound to arise. In such cases, the ability of PCBA manufacturers to respond swiftly and collaborate effectively is crucial.
6. Allowing Manufacturers Adequate Profit When Purchasing PCBA
With the rapid advancement of the circuit board and PCBA processing industries, PCBA pricing has become very transparent. A little research or comparison can help avoid being overcharged. Profit drives a company’s ability to serve customers; without profit, service quality and control diminish. Therefore, while purchasing PCBA, it’s essential to move beyond the mindset of relentless price bargaining and provide reasonable profits to PCBA manufacturers, benefiting the overall quality of your products and your own interests.
[Anti-Static Precautions During PCBA Processing]
When processing PCBA, personnel must meticulously follow the bill of materials, PCB silkscreen, and outsourcing requirements when inserting or mounting components. However, electronic components often generate static electricity, which, if not managed, can lead to electromagnetic pulses during discharge, causing computation errors and potentially damaging devices and circuits. Implementing anti-static measures is crucial to protect both machines and components. Here are some strategies to prevent static electricity:
1. All personnel handling components and products should wear anti-static clothing, bracelets, and shoes.
2. The anti-static system must include a reliable grounding device, with the anti-static ground wire kept separate from the power neutral wire and lightning protection ground.
3. Treat all components as electrostatic sensitive devices.
4. Use anti-static work surfaces and containers for components and semi-finished products during operations.
5. Ensure welding equipment is properly grounded, and electric soldering irons are anti-static types that must be tested before use.
6. Warehouse personnel should wear anti-static gloves during material handling and IQC testing, using grounded meters and covering work surfaces with anti-static rubber pads.
7. Regularly inspect all anti-static tools, setups, and materials to ensure they meet required conditions.
If you have any PCB manufacturing needs, please do not hesitate to contact me.Contact me