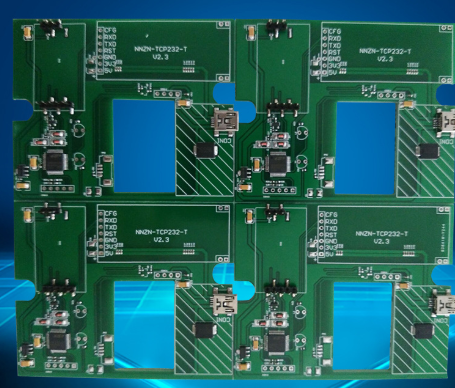
1. **Shellac Photosensitive Mask:** This oldest technology, introduced from the former Soviet Union, was quickly phased out due to the complexity of the ethanol development process.
2. **Bone Glue Photosensitive Mask:** This technology was adapted from the plate-making and sign-making processes, proving economical and practical. Subsequently, technicians developed physical solid film and chemical solid film technologies, which gained rapid promotion; however, they struggled with long-term storage at high temperatures.
3. **Polyvinyl Alcohol Photosensitive Mask:** This mask type can remain functional for over a month after preparation, with stable physical and chemical properties, marking a significant improvement over the bone glue mask.
None of these three mask types could meet the continuously evolving market demands. At that time, most printed circuit board graphics featured lines wider than 1.5mm, highlighting the urgent need for a new processing method.
2. **Self-Made Screen Printing Anti-Corrosion Ink:** The screens in use at that time were all silk screens, with limited mesh specifications. The predominant plate-making methods employed were “red-engraved film” and “etched pattern spray paint reversal.” Two primary formulations for self-made screen printing anti-corrosion inks emerged:
1. **Self-Drying Type:**
– Petroleum Bitumen: 200–300g
– Talcum Powder: 50–200g
– Dry Oil: 10–15ml
– Add Solvent Gasoline to 1000ml
2. **Drying Type:**
– Thick Paint: 150–200g
– Talcum Powder: 20–50g
– Color Material: 0.5–1g
– Rosin: 20–30g
– Add Turpentine Oil to 1000ml
– Condition: 130°C for 30 minutes
Although the self-made screen printing anti-corrosion ink had numerous shortcomings, it represented a significant advancement for PCB graphic manufacturing in China.
3. **Commercialization of Screen Printing Anti-Corrosion Ink:** Ink vendors recognized the robust business potential in China’s PCB ink market and rapidly introduced a variety of models and performance-specific screen printing anti-corrosive inks, leading to the establishment of a thriving printed board ink market. Companies from Hong Kong, Japan, and the United States quickly promoted their PCB screen printing anti-corrosion inks in China and established joint ventures. These branded inks exhibited stable performance and ease of use. A notable advancement was the introduction of an alkaline solution method for ink removal, which eliminated the need for solvent cleaning and reduced associated pollution.
With the rise of TV boards and tape recorder boards, UV curing type anti-corrosive screen printing inks emerged, significantly increasing PCB production speed. This ink boasted 100% solvent-free solid content, making it the preferred material for circuit board graphics processing. It is expected to see widespread promotion across the country within 1 to 2 years. At one point, there was a short supply of this ink, creating vast business opportunities for manufacturers.