1. PCB corrosion is a natural process in which unstable materials, such as metals, undergo chemical reactions that gradually destroy them and make them more stable.
2. Rust is a common result of this process, particularly in iron and iron alloys exposed to a combination of oxygen and moisture.
3. Corrosion can be caused by various factors, including atmospheric corrosion, localized corrosion, electrical corrosion, and electrolytic corrosion.
4. During maintenance, equipment failures caused by PCB corrosion are often observed.
5. Sometimes, a component may be accidentally sprayed, soaked, or immersed in liquid, leading to gradual and unexpected corrosion.

Reasons for PCB Corrosion
1. Temperature changes
Rapid temperature changes can cause condensation within the electrical enclosure, ultimately leading to corrosion related faults. When warm and humid air is suddenly exposed to a surface below the dew point temperature of the surrounding air, condensation occurs. This will lead to gradual corrosion of component metals (commonly copper, lead, and tin in printed circuit boards).
2. Chemical processes
Some circuit board manufacturing processes involve chemicals that may accelerate the corrosion process. One example is when a circuit board is exposed to acid, such as nitric acid (usually used in fertilizers) or citric acid (used as a very common food preservative). This is a bit difficult to avoid as it is very dependent on the application. Discuss and develop a written plan with your employees to control processes involving corrosive chemicals. Ensure that your employees follow the correct procedures to distribute and use these substances around your machine.
3. Atmospheric corrosion
A common problem with circuit boards is atmospheric corrosion, where metals are exposed to moisture, which in turn exposes them to oxygen, leading to the reaction of metal ions bonding with oxygen atoms to form oxides. Atmospheric corrosion mainly occurs on copper components. Although corrosion of copper does not affect the mechanical properties of circuit boards, it can affect their conductivity.
4. Material defects
During the manufacturing process of circuit boards, there may be material defects such as bubbles, notches, holes, etc. These defects can make the surface of the circuit board susceptible to corrosion and erosion.
The Manifestations of PCB Corrosion
The manifestations of PCB corrosion include the following aspects:
1. The surface of the circuit board may show corrosion spots, pits, etc., which can cause circuit interruption in severe cases.
2. The metal wires or solder joints on the circuit board are prone to corrosion damage, forming virtual open circuits or short circuits.
3. The components or devices on the surface of the circuit board are prone to corrosion and erosion, leading to performance degradation or failure.
Methods to Avoid PCB Corrosion
1. Control humidity and temperature: During the manufacturing process of circuit boards, it is necessary to control the temperature and humidity of the products to avoid corrosion caused by environmental factors.
2. Choose high-quality materials: High quality materials have good corrosion resistance, so it is necessary to choose high-quality materials when manufacturing circuit boards.
3. Control the amount and concentration of chemicals: When conducting chemical treatment on the surface of circuit boards, it is necessary to control the amount and concentration of chemicals to avoid corrosion.
4. Strengthen maintenance and upkeep: It is necessary to strengthen maintenance and upkeep of already manufactured circuit boards, and regularly clean and repair them to ensure that there is no corrosion on the surface of the circuit board.
By taking the above measures, the occurrence of PCB corrosion can be effectively avoided, thereby enhancing the reliability and stability of the circuit board and ensuring its normal use.
PCB corrosion is the main cause of electronic product failures. At first, the effect of corrosion was to increase the resistance of copper traces on the circuit board, but as the degree of corrosion increased, the working efficiency of the PCB would decrease or even stop working.
For more information, click the website: wellcircuits.com
To enhance Your Business Efficiency, contact us:
To discover How Our Solutions Can Help Your Business, contact us:
Stay Ahead in Your Industry – Subscribe to Our Latest News
Customized Solutions Await Discovery – Contact Our Sales Team
Don’t Miss Critical Updates – Subscribe to us now
2. Rust is a common result of this process, particularly in iron and iron alloys exposed to a combination of oxygen and moisture.
3. Corrosion can be caused by various factors, including atmospheric corrosion, localized corrosion, electrical corrosion, and electrolytic corrosion.
4. During maintenance, equipment failures caused by PCB corrosion are often observed.
5. Sometimes, a component may be accidentally sprayed, soaked, or immersed in liquid, leading to gradual and unexpected corrosion.
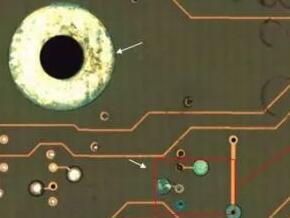
Reasons for PCB Corrosion
1. Temperature changes
Rapid temperature changes can cause condensation within the electrical enclosure, ultimately leading to corrosion related faults. When warm and humid air is suddenly exposed to a surface below the dew point temperature of the surrounding air, condensation occurs. This will lead to gradual corrosion of component metals (commonly copper, lead, and tin in printed circuit boards).
2. Chemical processes
Some circuit board manufacturing processes involve chemicals that may accelerate the corrosion process. One example is when a circuit board is exposed to acid, such as nitric acid (usually used in fertilizers) or citric acid (used as a very common food preservative). This is a bit difficult to avoid as it is very dependent on the application. Discuss and develop a written plan with your employees to control processes involving corrosive chemicals. Ensure that your employees follow the correct procedures to distribute and use these substances around your machine.
3. Atmospheric corrosion
A common problem with circuit boards is atmospheric corrosion, where metals are exposed to moisture, which in turn exposes them to oxygen, leading to the reaction of metal ions bonding with oxygen atoms to form oxides. Atmospheric corrosion mainly occurs on copper components. Although corrosion of copper does not affect the mechanical properties of circuit boards, it can affect their conductivity.
4. Material defects
During the manufacturing process of circuit boards, there may be material defects such as bubbles, notches, holes, etc. These defects can make the surface of the circuit board susceptible to corrosion and erosion.
The Manifestations of PCB Corrosion
The manifestations of PCB corrosion include the following aspects:
1. The surface of the circuit board may show corrosion spots, pits, etc., which can cause circuit interruption in severe cases.
2. The metal wires or solder joints on the circuit board are prone to corrosion damage, forming virtual open circuits or short circuits.
3. The components or devices on the surface of the circuit board are prone to corrosion and erosion, leading to performance degradation or failure.
Methods to Avoid PCB Corrosion
1. Control humidity and temperature: During the manufacturing process of circuit boards, it is necessary to control the temperature and humidity of the products to avoid corrosion caused by environmental factors.
2. Choose high-quality materials: High quality materials have good corrosion resistance, so it is necessary to choose high-quality materials when manufacturing circuit boards.
3. Control the amount and concentration of chemicals: When conducting chemical treatment on the surface of circuit boards, it is necessary to control the amount and concentration of chemicals to avoid corrosion.
4. Strengthen maintenance and upkeep: It is necessary to strengthen maintenance and upkeep of already manufactured circuit boards, and regularly clean and repair them to ensure that there is no corrosion on the surface of the circuit board.
By taking the above measures, the occurrence of PCB corrosion can be effectively avoided, thereby enhancing the reliability and stability of the circuit board and ensuring its normal use.
PCB corrosion is the main cause of electronic product failures. At first, the effect of corrosion was to increase the resistance of copper traces on the circuit board, but as the degree of corrosion increased, the working efficiency of the PCB would decrease or even stop working.
For more information, click the website: wellcircuits.com
To enhance Your Business Efficiency, contact us:
To discover How Our Solutions Can Help Your Business, contact us:
Stay Ahead in Your Industry – Subscribe to Our Latest News
Customized Solutions Await Discovery – Contact Our Sales Team
Don’t Miss Critical Updates – Subscribe to us now