As the demand for FPC connectors increases, the performance technology surrounding them continues to evolve. Whether you are a user or a manufacturer of FPC connectors, do you truly understand their intricacies? Are you aware of the performance technologies they encompass? Allow me to introduce you to the key performance technologies of FPC connectors.
The utilization of FPC connectors is on the rise, closely intertwined with modern life. From the standpoint of connector performance technology and practicality, these connectors are extensively used in digital devices, automotive audio systems, and medical equipment. Today, high-quality connectors have become essential for the efficient operation of specialized equipment that enhances our quality of life. Below, I will explain the performance technologies associated with FPC connectors.
FPC connectors feature a high density, compact volume, and lightweight design. Typically, an FPC connector measures 1.0mm in thickness, 3.2mm in depth, with a terminal pitch of 0.6mm. They are commonly found in LCD displays, scanners, telecommunication cards, memory devices, mobile hard drives, audio systems, digital cameras, car audio systems, televisions, typewriters, calculators, cash registers, telephones, and various other equipment.
—
Let me know if you need any further adjustments!
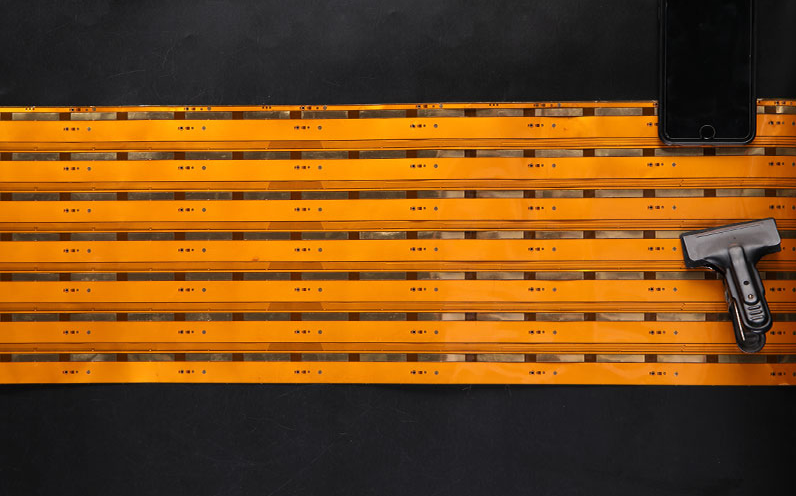
1. From the perspective of electronic market applications, FPC connectors currently primarily feature a pitch of 0.5mm, with 0.3mm pitch products also seeing widespread adoption. On one hand, the trend in the electronic product market is towards miniaturization. On the other hand, the integration of numerous functional modules into systems is increasing the number of signals that need to be transmitted. This necessitates more pins, leading to a demand for FPC connectors with additional contacts or even smaller configurations. With reduced spacing and a more compact design, products are evolving towards high-density integration.
2. FPC connectors are rapidly advancing in miniaturization within electronic devices, particularly smartphones. They have emerged as a primary connection method using flexible circuits to link circuit boards in consumer electronics. In the automotive sector, FFC connectors are extensively used in radios, GPS devices, LCD displays, and entertainment systems. Regarding medical equipment, FFC/FPC connectors facilitate the necessary miniaturization for handheld devices, including monitors, and their applications are becoming increasingly common.
3. The stability and reliability of FPC connectors are the most critical performance indicators. This requires careful design considerations, encompassing aspects such as plastic mold flow, terminal performance, contact force, and connector covers before mass production. Designers should employ various software tools for thorough and comprehensive analyses to assess strength and structure, ensuring connector quality and design reliability. Additionally, during the manufacturing process, the use of semi-automatic or fully automatic assembly, inspection, and packaging significantly reduces manual intervention, thereby minimizing potential quality issues.
4. A key advantage of FPC connectors lies in their efficient utilization of available space, both on the PCB and within the housing. This not only helps reduce costs but also encourages compact and high-mobility designs, making them widely applicable across various segments of the electronics market. Another benefit of FPC connectors is their ability to provide interconnections for moving components. For instance, the display of a digital camera can be extended or flexibly adjusted while maintaining an electrical connection to the camera body, or the display of a laptop or mobile phone can flip or slide while staying connected to the device.
5. The above outlines relevant insights into various performance technologies related to FPC connectors.
—
Let me know if you need any more adjustments!