As the yield ratio of flexible PCBs continues to improve, and the adoption of rigid-flex PCBs becomes more widespread, the terminology surrounding PCBs has evolved. Today, it’s common to refer to PCBs by their mechanical properties such as softness, rigidity, or rigid-flexibility, alongside specific layer configurations. Flexible PCBs (FPCs) made from soft insulating substrates are often referred to as “soft FPCs” or “flexible FPCs,” while rigid-flex composite PCBs are known as “rigid-flex PCBs.” These technologies address the growing demands of modern electronic products, including high density, high reliability, miniaturization, and lightweight designs. Furthermore, they meet stringent economic requirements and contribute to the competitiveness of the market and technology landscape.
Flexible PCBs first gained widespread use in the early 1960s in foreign markets. In China, however, the production and application of flexible PCBs began only in the mid-1960s. In recent years, with the acceleration of global economic integration and market liberalization, the adoption of imported technologies has surged. As a result, some small and medium-sized rigid-FPC manufacturers have seized this opportunity to integrate both soft and hard technologies. By leveraging existing equipment, these manufacturers have enhanced their tooling and production processes to better align with the increasing demand for flexible PCBs.
To gain a deeper understanding of PCB technology, particularly the soft PCB process, this article provides an introductory overview. By examining the key developments and advancements in flexible PCB manufacturing, we can better grasp the industry’s evolving trends and the associated challenges in meeting the dynamic demands of modern electronics.

**Classification of Flexible PCBs and Their Advantages and Disadvantages**
Flexible printed circuit boards (PCBs) are an essential component in modern electronics due to their versatility, lightweight nature, and ability to conform to compact and complex designs. They are typically categorized based on their structure, conductor layers, and applications. Here, we will explore the different types of flexible PCBs, their unique features, and the advantages and disadvantages of each.
### 1. Flexible PCB Classification
Flexible PCBs are primarily classified according to the number of conductor layers and their structural configuration. The main categories are as follows:
#### 1.1 **Single-Sided Flexible PCB**
A single-sided flexible PCB has only one conductive layer. The insulation material varies based on the specific application, with common materials including polyester, polyimide, polytetrafluoroethylene (PTFE), and soft epoxy-glass cloth. This type of PCB can be further subdivided into the following types:
1. **Single-Sided Connection without Covering Layer**
– **Description**: In this type, the conductor pattern is applied directly on the insulating substrate, without any covering layer. This design is cost-effective and typically used in non-critical applications where environmental protection is not a significant concern.
– **Applications**: Early telecommunication devices, low-cost electronics.
– **Advantages**: Low cost, simple design.
– **Disadvantages**: Less durable and vulnerable to environmental factors like moisture and dirt.
2. **Single-Sided Connection with Covering Layer**
– **Description**: This type adds a protective covering over the conductive layer, typically designed to protect the traces from damage and improve durability. The pads remain exposed to allow for component mounting.
– **Applications**: Automotive instrumentation, consumer electronics.
– **Advantages**: Better protection of the conductor traces, enhanced durability.
– **Disadvantages**: Slightly more expensive than the non-covered version due to additional manufacturing steps.
3. **Double-Sided Connection without Covering Layer**
– **Description**: This design allows for connections to be made on both the front and back sides of the flexible PCB, typically through via holes drilled into the insulating material. These vias are created using punching, etching, or mechanical processes.
– **Applications**: Devices requiring dual-sided mounting or where both sides need to be soldered.
– **Advantages**: Increased component density and functionality.
– **Disadvantages**: More complex to manufacture, may have reduced flexibility compared to single-sided designs.
4. **Double-Sided Connection with Covering Layer**
– **Description**: Similar to the previous type but with the addition of a covering layer. Vias are incorporated into the cover to maintain electrical insulation while still allowing both sides to be interconnected.
– **Applications**: Applications requiring both high durability and dual-sided connections, such as in more advanced automotive or aerospace electronics.
– **Advantages**: Durability, dual-sided functionality.
– **Disadvantages**: Higher cost due to additional layers and manufacturing complexity.
#### 1.2 **Double-Sided Flexible PCB**
A double-sided flexible PCB consists of two conductive layers. This design increases the wiring density per unit area compared to single-sided designs. It can be further classified based on the presence or absence of metallized holes and covering layers:
– **Without Metallized Holes and Without Covering Layer**
– **Without Metallized Holes and With Covering Layer**
– **With Metallized Holes and Without Covering Layer**
– **With Metallized Holes and With Covering Layer**
**Advantages**: Double-sided flexible PCBs allow for more complex circuits, increased wiring density, and can support more components in the same physical area.
**Disadvantages**: The absence of a covering layer in certain designs can expose the PCB to environmental risks. Additionally, the presence of metallized holes complicates the manufacturing process and increases costs.
#### 1.3 **Multilayer Flexible PCB**
Multilayer flexible PCBs use a lamination technique to integrate multiple layers of conductive material and insulating material, resulting in a flexible yet complex circuit structure. These boards are often used in high-performance applications, where space and weight are at a premium.
– **Common Structures**: The simplest form of a multilayer flexible PCB is a three-layer design, where two copper shielding layers are added to a single-sided PCB. More commonly, a four-layer structure is used, with metallized holes enabling interlayer connections. The two middle layers typically serve as power and ground planes.
**Advantages**:
– **Lightweight**: Multilayer flexible PCBs, particularly those made from polyimide, are lighter than their rigid counterparts made from epoxy glass cloth.
– **Electrical Properties**: They offer excellent electrical performance, such as low dielectric constants, which are beneficial for high-speed signal transmission.
– **Space Efficiency**: By using multiple layers, these PCBs allow for more components to be placed in a smaller footprint.
**Disadvantages**:
– **Cost**: The complexity of the manufacturing process for multilayer PCBs makes them more expensive.
– **Reduced Flexibility**: While still flexible, multilayer PCBs may not offer the same level of flexibility as single-sided or double-sided designs.
### Conclusion
Flexible PCBs are indispensable in a wide range of industries, offering both performance and versatility in compact designs. The choice of which type to use depends on specific application requirements such as cost, density, durability, and flexibility. Single-sided flexible PCBs are often the most cost-effective for simpler applications, while multilayer flexible PCBs provide enhanced functionality and electrical properties for more advanced, high-performance devices. Each type has its own set of advantages and trade-offs, making it crucial for engineers to carefully select the most suitable design based on the demands of the end product.
Flexible PCBs first gained widespread use in the early 1960s in foreign markets. In China, however, the production and application of flexible PCBs began only in the mid-1960s. In recent years, with the acceleration of global economic integration and market liberalization, the adoption of imported technologies has surged. As a result, some small and medium-sized rigid-FPC manufacturers have seized this opportunity to integrate both soft and hard technologies. By leveraging existing equipment, these manufacturers have enhanced their tooling and production processes to better align with the increasing demand for flexible PCBs.
To gain a deeper understanding of PCB technology, particularly the soft PCB process, this article provides an introductory overview. By examining the key developments and advancements in flexible PCB manufacturing, we can better grasp the industry’s evolving trends and the associated challenges in meeting the dynamic demands of modern electronics.
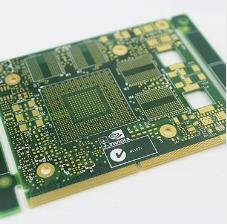
**Classification of Flexible PCBs and Their Advantages and Disadvantages**
Flexible printed circuit boards (PCBs) are an essential component in modern electronics due to their versatility, lightweight nature, and ability to conform to compact and complex designs. They are typically categorized based on their structure, conductor layers, and applications. Here, we will explore the different types of flexible PCBs, their unique features, and the advantages and disadvantages of each.
### 1. Flexible PCB Classification
Flexible PCBs are primarily classified according to the number of conductor layers and their structural configuration. The main categories are as follows:
#### 1.1 **Single-Sided Flexible PCB**
A single-sided flexible PCB has only one conductive layer. The insulation material varies based on the specific application, with common materials including polyester, polyimide, polytetrafluoroethylene (PTFE), and soft epoxy-glass cloth. This type of PCB can be further subdivided into the following types:
1. **Single-Sided Connection without Covering Layer**
– **Description**: In this type, the conductor pattern is applied directly on the insulating substrate, without any covering layer. This design is cost-effective and typically used in non-critical applications where environmental protection is not a significant concern.
– **Applications**: Early telecommunication devices, low-cost electronics.
– **Advantages**: Low cost, simple design.
– **Disadvantages**: Less durable and vulnerable to environmental factors like moisture and dirt.
2. **Single-Sided Connection with Covering Layer**
– **Description**: This type adds a protective covering over the conductive layer, typically designed to protect the traces from damage and improve durability. The pads remain exposed to allow for component mounting.
– **Applications**: Automotive instrumentation, consumer electronics.
– **Advantages**: Better protection of the conductor traces, enhanced durability.
– **Disadvantages**: Slightly more expensive than the non-covered version due to additional manufacturing steps.
3. **Double-Sided Connection without Covering Layer**
– **Description**: This design allows for connections to be made on both the front and back sides of the flexible PCB, typically through via holes drilled into the insulating material. These vias are created using punching, etching, or mechanical processes.
– **Applications**: Devices requiring dual-sided mounting or where both sides need to be soldered.
– **Advantages**: Increased component density and functionality.
– **Disadvantages**: More complex to manufacture, may have reduced flexibility compared to single-sided designs.
4. **Double-Sided Connection with Covering Layer**
– **Description**: Similar to the previous type but with the addition of a covering layer. Vias are incorporated into the cover to maintain electrical insulation while still allowing both sides to be interconnected.
– **Applications**: Applications requiring both high durability and dual-sided connections, such as in more advanced automotive or aerospace electronics.
– **Advantages**: Durability, dual-sided functionality.
– **Disadvantages**: Higher cost due to additional layers and manufacturing complexity.
#### 1.2 **Double-Sided Flexible PCB**
A double-sided flexible PCB consists of two conductive layers. This design increases the wiring density per unit area compared to single-sided designs. It can be further classified based on the presence or absence of metallized holes and covering layers:
– **Without Metallized Holes and Without Covering Layer**
– **Without Metallized Holes and With Covering Layer**
– **With Metallized Holes and Without Covering Layer**
– **With Metallized Holes and With Covering Layer**
**Advantages**: Double-sided flexible PCBs allow for more complex circuits, increased wiring density, and can support more components in the same physical area.
**Disadvantages**: The absence of a covering layer in certain designs can expose the PCB to environmental risks. Additionally, the presence of metallized holes complicates the manufacturing process and increases costs.
#### 1.3 **Multilayer Flexible PCB**
Multilayer flexible PCBs use a lamination technique to integrate multiple layers of conductive material and insulating material, resulting in a flexible yet complex circuit structure. These boards are often used in high-performance applications, where space and weight are at a premium.
– **Common Structures**: The simplest form of a multilayer flexible PCB is a three-layer design, where two copper shielding layers are added to a single-sided PCB. More commonly, a four-layer structure is used, with metallized holes enabling interlayer connections. The two middle layers typically serve as power and ground planes.
**Advantages**:
– **Lightweight**: Multilayer flexible PCBs, particularly those made from polyimide, are lighter than their rigid counterparts made from epoxy glass cloth.
– **Electrical Properties**: They offer excellent electrical performance, such as low dielectric constants, which are beneficial for high-speed signal transmission.
– **Space Efficiency**: By using multiple layers, these PCBs allow for more components to be placed in a smaller footprint.
**Disadvantages**:
– **Cost**: The complexity of the manufacturing process for multilayer PCBs makes them more expensive.
– **Reduced Flexibility**: While still flexible, multilayer PCBs may not offer the same level of flexibility as single-sided or double-sided designs.
### Conclusion
Flexible PCBs are indispensable in a wide range of industries, offering both performance and versatility in compact designs. The choice of which type to use depends on specific application requirements such as cost, density, durability, and flexibility. Single-sided flexible PCBs are often the most cost-effective for simpler applications, while multilayer flexible PCBs provide enhanced functionality and electrical properties for more advanced, high-performance devices. Each type has its own set of advantages and trade-offs, making it crucial for engineers to carefully select the most suitable design based on the demands of the end product.