PCB board design plays a crucial role in ensuring the functionality and manufacturability of a circuit. With PCB design software, we can define a wide range of design rules that help maintain the integrity of the design throughout the development process. Typically, design rules are established at the start of the design process, and they serve as guidelines for verifying and refining the design once the initial layout is completed.
In previous tutorials, we explored routing design rules and added a width constraint rule. Additionally, we observed that PCB Board Wizard already contains some predefined design rules. These rules serve as a foundation for ensuring that the layout adheres to industry standards and functional requirements.
To verify that the PCB layout complies with these design rules, we perform a Design Rule Check (DRC), which helps identify potential issues before moving to the manufacturing stage. Below is a structured approach to performing the DRC:
### Step-by-Step Guide to Performing DRC:
1. **Enable DRC Error Markers**
First, go to **Design >> Board Layers & Colors** (shortcut key: **L**) and make sure the **Show** button in the **DRC Error Markers** option under the **System Colors** section is checked. This ensures that any design rule violations are clearly displayed on the layout as error markers, making it easier to spot issues.
2. **Configure Design Rule Checker**
Next, navigate to **Tools >> Design Rule Check** (shortcut keys: **T, D**) to open the Design Rule Checker dialog box. Ensure that both real-time and batch DRC checks are properly configured. Real-time checks continuously validate the design as changes are made, while batch checks can be run at the end of the design process to identify cumulative issues.
3. **Check Specific Rule Categories**
In the DRC dialog box, select one of the categories, such as **Electrical**, to view all the specific rules associated with that category. These rules might cover aspects like trace width, clearances, and via sizes. Reviewing and addressing violations in each category ensures that the design meets both electrical and manufacturing requirements.
By following this structured approach, you can systematically verify that your PCB layout adheres to the defined design rules, helping you avoid common design errors and ensuring a successful and manufacturable final product.
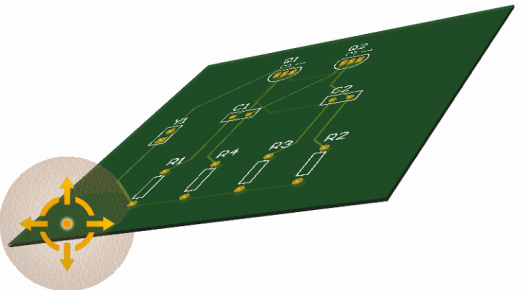
**3. Run Design Rule Check (DRC) and Identify Violations**
Start by keeping all options at their default settings and clicking the “Run Design Rule Check” button. The DRC process will begin, and the report file “Multivibrator.DRC” will open. Any errors will also be displayed in the information panel. By clicking on the highlighted error, we can navigate to the specific PCB area where the violation occurs. In this case, the pad of the transistor is highlighted in green, indicating a design rule violation.
**4. Analyzing the Error Report**
The information panel lists all design rule violations found in the PCB. Specifically, it shows that transistors Q1 and Q2 are violating the 13 mil minimum safety distance rule. There are four main types of violations listed under the removal constraints. Double-clicking the error message will automatically zoom in on the corresponding area in the PCB layout.
It’s a good practice to define safety distance rules before routing, considering factors like routing technology and the physical performance of the device. Now, let’s analyze the error, revisit our safety distance rules, and determine the best solution.
### **5. Measuring the Minimum Safety Distance**
To accurately determine the minimum safety distance between the pads of the transistors, follow these steps:
1. **Enlarge the View:** Select the PCB file, position the cursor over a transistor pad, and press the PAGE UP key to zoom in.
2. **Initiate Measurement Mode:** From the menu, go to Reports > Measure Primitives (shortcut: R, P). The cursor will change to a crosshair for measurement.
3. **Select the First Pad:** Click in the center of the transistor pad on the left side. A pop-up menu will appear, allowing you to select the pad.
4. **Select the Second Pad:** Next, position the cursor over the second transistor pad and press ENTER again. The minimum distance between the two pads will be displayed in an information box, showing 10.63 mils.
5. **Exit Measurement Mode:** Close the dialog box, press ESC or right-click to exit, and use the V and F shortcuts to adjust the scale of the view.
### **6. Reviewing Safety Distance Design Rules**
To understand the current safety distance rules:
1. Go to **Design > Rules** (shortcut: D, R) to open the PCB Rules and Constraints Editor.
2. Double-click the **Electrical** category to see all electrical rules.
3. Locate the **Safety Distance** rule, then click on **Clearance** to open it. The dialog box will display the default minimum safety distance for the entire PCB as 13 mils.
Since the minimum distance between the transistor pads is below this value, the DRC reports it as a violation.
### **7. Adjusting the Design Rule for Transistor Pads**
Given that the minimum distance is slightly over 10 mils, we can create a custom design rule for transistor pads specifically.
1. In the **Safety Clearance** section of the design rule folder, right-click and select **New Rule** to add a custom clearance constraint.
2. In the newly created rule (named **Clearance_1**), set the **Minimum Clearance** to 10 mils in the **Constraints** tab.
3. Click **Advanced (Query)**, then select **Query Helper** to define a conditional search. For the first object, use the condition:
`HasFootprintPad(‘TO-92A’,’*’)`
The asterisk (*) denotes any pad named “TO-92A.”
4. Keep the second object range as **ALL**, then click **OK**. Click **Apply** to save the changes, and **OK** to close the Rules Editor.
### **8. Re-run the DRC Check**
After adjusting the safety clearance rule, run the DRC again by selecting **Tools > Design Rule Check**. This time, there should be no violations, as the new rule allows for a 10 mil minimum clearance between the transistor pads.
### **9. Finalizing the PCB Design**
Finally, save the updated PCB and project files. Congratulations, your PCB layout is now complete, and you’re ready to generate the output files for manufacturing.
**Conclusion and Key Takeaways:**
– It’s crucial to define clear safety distance rules before starting PCB routing to avoid design rule violations.
– When violations occur, measuring the exact distance between pads helps ensure that the correct design rule adjustments are made.
– Customizing rules for specific components, like transistors, can help resolve violations without affecting the overall design.
– Always validate your changes by re-running the DRC after adjustments to ensure compliance.
By following these steps and maintaining a structured approach to design rule management, you can ensure a smooth and efficient PCB layout process.