The following article discusses the maintenance and upkeep methods for horizontal and vertical electroplating wires commonly utilized in PCB manufacturing. It highlights both the similarities and differences between these two types of electroplating equipment, covering the maintenance protocols for their tanks, conveying mechanisms, circulating filtration systems, electrical systems, and piping systems, as well as the procedures for long-term equipment shutdowns.
In the printed circuit board production process, the quality of the plating layer significantly influences the subsequent etching phase, making the integrity of the plating layer crucial for the overall quality of the circuit board. Electroplating equipment represents a substantial investment for PCB manufacturers. To ensure the smooth operation, stability, and longevity of this equipment, proper maintenance practices are essential. This article focuses on the maintenance strategies for electroplating equipment frequently employed in printed circuit board production.
1. Types of Equipment
In PCB production, there are primarily two types of electroplating systems: horizontal electroplating lines and vertical electroplating lines. The main distinction between these systems lies in how the PCB boards are transported, which also leads to differences in the structure of the conveying equipment, thereby resulting in slightly varied maintenance requirements.
2. Daily Maintenance and Upkeep Methods
2.1. Tank Maintenance
The key difference between vertical and horizontal plating lines is the method of circuit board transportation; however, their tank maintenance procedures are fundamentally similar. Every 7 days, the pickling tank should be cleaned and the bath liquid replaced. Inspect the tank’s spray device for any blockages and clear any obstructions promptly. For the conductive supports in the copper plating tank, tin plating tank, and at the contact points of the anode and live wire, use a rag and sandpaper for cleaning. During inspections, replace any deteriorated titanium basket bags and tin strip baskets, and add copper balls and tin strips as needed. After introducing new copper balls and tin strips, conduct electrolysis in both the copper and tin electroplating baths to stabilize production performance. Every 90 days, clean the copper ball and anode bag, and utilize activated carbon for filtering and cleaning the bath every 120 to 150 days to remove impurities, also performing a clean of the tin bath.
2.2. Maintenance of the Vibration Mechanism in Vertical Electroplating Lines
In vertical electroplating, to ensure uniform surface copper deposition and effective hole filling, a vibrating mechanism is employed within the tank. Every 30 days, check the reducer for normal operation and inspect its tightness; verify the tightness of the vibration mounting motor bolts; and assess the wear on the vibration rubber, replacing it if it shows significant wear. At 180-day intervals, examine the power cord connections in the junction box; if any connectors are loose, tighten them immediately. Additionally, replace any power cords with melted or aging insulation to maintain safety. All bearings in the vibrating mechanism should be inspected, with severely worn bearings replaced promptly during lubrication.
2.3. Maintenance of Cranes in Vertical Electroplating Lines
Vertical electroplating lines utilize cranes and hangers for circuit board transport. It is recommended to clean both the crane and the hanger weekly (without disassembly) to maintain a neat appearance. Use a rag for wiping and sandpaper for polishing. Every 30 days, conduct a check on the hanger for any damage, and perform maintenance on the crane’s motor and reducer, ensuring the entire transmission system operates smoothly. After 180 days, carry out a thorough cleaning and maintenance of the crane and hanging equipment, removing the hanging equipment from the crane for comprehensive cleaning.

**2.4. Maintenance of the Horizontal Electroplating Line Conveying Device**
The conveying device used in the horizontal electroplating line consists of rollers, which utilize their rotation to continuously transport circuit boards into each tank. Consequently, the maintenance of the horizontal electroplating line conveying device is similar to that of the vertical electroplating line, with some distinctions.
Every **7 days**, clean the rollers of the horizontal electroplating line to remove any foreign matter, ensuring that the circuit board’s surface remains clean during transport. Additionally, check the coupling for any looseness. Every **180 days**, inspect the rollers for wear; replace any worn rollers promptly to prevent jamming during transport. Furthermore, the transmission gear, transmission shaft, and the entire transmission system should be regularly inspected, with any arising issues addressed promptly.
**2.5. Maintenance of the Circulating Filter System**
Every **7 days**, inspect the filter cartridge of the circulating filter system for any leaks. The filter core should be cleaned or replaced every **10 to 15 days**. Every **30 days**, replace the filter carbon core to ensure optimal filter quality and flow rate; clean the filter pump, as well as the filter hood and screen of the air pump. Also, check the condition of the pump motor power cord connector every **30 days**. If any looseness is detected, tighten it immediately; replace any aging wires to ensure good contact and safe insulation to protect the motor.
**2.6. Maintenance of Other Parts**
Every **7 days**, check the output power of the power supply twice. Inspect the power supply, electrical control heat dissipation, and radiator for dust accumulation, cleaning as necessary to maintain effective heat dissipation. Every **30 days**, examine the electrical components of the control unit, replacing any damaged or corroded parts. Inspect all connectors, repairing any poor contacts, virtual connections, or faulty soldering; replace any rusted or damaged connectors promptly. Additionally, check all contactors and relays; replace them if bad contacts or sticking issues are identified. Assess the main parameters of capacitors, reactors, resistors, and other components, replacing any that show abnormalities as soon as possible.
For the automatic feeding system, perform a check and calibration every **7 days**. Also, clean the scale and dirt on the electric heater every **7 days** to prevent excessive internal temperature buildup.
For all water and gas piping systems, conduct checks every **7 days** to identify any leaks or fluid escapes, and promptly repair or replace any faulty pipes.
**3. Maintenance Before Long-Term Shutdown**
If the equipment is scheduled for long-term shutdown, it must be properly maintained to prevent corrosion and aging during the idle period. Actions to take include: clean the floor, removing any water to keep it dry, and ensure the machine platform, tanks, drive systems, and hangers are clean and dry. Wrap all motors in plastic for protection; lubricate all bearings with grease to prevent rust; clean all pipelines thoroughly; and clean the filter barrel and its elements. Lastly, ensure all heaters in the tanks are cleaned to remove any dirt and kept dry.
The electroplating equipment used in printed circuit board production can vary significantly due to different production processes and manufacturers. As a result, maintenance methods may also differ. However, timely and correct maintenance should never be overlooked due to production schedules or output pressures. Only through proper and timely maintenance can the equipment’s normal operation and stable performance be ensured, ultimately safeguarding production quality and output.
In the printed circuit board production process, the quality of the plating layer significantly influences the subsequent etching phase, making the integrity of the plating layer crucial for the overall quality of the circuit board. Electroplating equipment represents a substantial investment for PCB manufacturers. To ensure the smooth operation, stability, and longevity of this equipment, proper maintenance practices are essential. This article focuses on the maintenance strategies for electroplating equipment frequently employed in printed circuit board production.
1. Types of Equipment
In PCB production, there are primarily two types of electroplating systems: horizontal electroplating lines and vertical electroplating lines. The main distinction between these systems lies in how the PCB boards are transported, which also leads to differences in the structure of the conveying equipment, thereby resulting in slightly varied maintenance requirements.
2. Daily Maintenance and Upkeep Methods
2.1. Tank Maintenance
The key difference between vertical and horizontal plating lines is the method of circuit board transportation; however, their tank maintenance procedures are fundamentally similar. Every 7 days, the pickling tank should be cleaned and the bath liquid replaced. Inspect the tank’s spray device for any blockages and clear any obstructions promptly. For the conductive supports in the copper plating tank, tin plating tank, and at the contact points of the anode and live wire, use a rag and sandpaper for cleaning. During inspections, replace any deteriorated titanium basket bags and tin strip baskets, and add copper balls and tin strips as needed. After introducing new copper balls and tin strips, conduct electrolysis in both the copper and tin electroplating baths to stabilize production performance. Every 90 days, clean the copper ball and anode bag, and utilize activated carbon for filtering and cleaning the bath every 120 to 150 days to remove impurities, also performing a clean of the tin bath.
2.2. Maintenance of the Vibration Mechanism in Vertical Electroplating Lines
In vertical electroplating, to ensure uniform surface copper deposition and effective hole filling, a vibrating mechanism is employed within the tank. Every 30 days, check the reducer for normal operation and inspect its tightness; verify the tightness of the vibration mounting motor bolts; and assess the wear on the vibration rubber, replacing it if it shows significant wear. At 180-day intervals, examine the power cord connections in the junction box; if any connectors are loose, tighten them immediately. Additionally, replace any power cords with melted or aging insulation to maintain safety. All bearings in the vibrating mechanism should be inspected, with severely worn bearings replaced promptly during lubrication.
2.3. Maintenance of Cranes in Vertical Electroplating Lines
Vertical electroplating lines utilize cranes and hangers for circuit board transport. It is recommended to clean both the crane and the hanger weekly (without disassembly) to maintain a neat appearance. Use a rag for wiping and sandpaper for polishing. Every 30 days, conduct a check on the hanger for any damage, and perform maintenance on the crane’s motor and reducer, ensuring the entire transmission system operates smoothly. After 180 days, carry out a thorough cleaning and maintenance of the crane and hanging equipment, removing the hanging equipment from the crane for comprehensive cleaning.
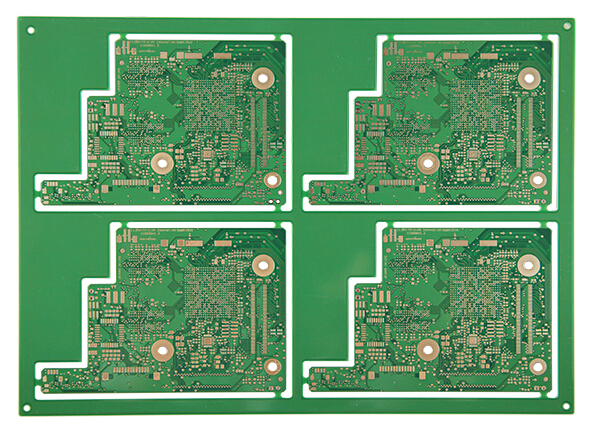
**2.4. Maintenance of the Horizontal Electroplating Line Conveying Device**
The conveying device used in the horizontal electroplating line consists of rollers, which utilize their rotation to continuously transport circuit boards into each tank. Consequently, the maintenance of the horizontal electroplating line conveying device is similar to that of the vertical electroplating line, with some distinctions.
Every **7 days**, clean the rollers of the horizontal electroplating line to remove any foreign matter, ensuring that the circuit board’s surface remains clean during transport. Additionally, check the coupling for any looseness. Every **180 days**, inspect the rollers for wear; replace any worn rollers promptly to prevent jamming during transport. Furthermore, the transmission gear, transmission shaft, and the entire transmission system should be regularly inspected, with any arising issues addressed promptly.
**2.5. Maintenance of the Circulating Filter System**
Every **7 days**, inspect the filter cartridge of the circulating filter system for any leaks. The filter core should be cleaned or replaced every **10 to 15 days**. Every **30 days**, replace the filter carbon core to ensure optimal filter quality and flow rate; clean the filter pump, as well as the filter hood and screen of the air pump. Also, check the condition of the pump motor power cord connector every **30 days**. If any looseness is detected, tighten it immediately; replace any aging wires to ensure good contact and safe insulation to protect the motor.
**2.6. Maintenance of Other Parts**
Every **7 days**, check the output power of the power supply twice. Inspect the power supply, electrical control heat dissipation, and radiator for dust accumulation, cleaning as necessary to maintain effective heat dissipation. Every **30 days**, examine the electrical components of the control unit, replacing any damaged or corroded parts. Inspect all connectors, repairing any poor contacts, virtual connections, or faulty soldering; replace any rusted or damaged connectors promptly. Additionally, check all contactors and relays; replace them if bad contacts or sticking issues are identified. Assess the main parameters of capacitors, reactors, resistors, and other components, replacing any that show abnormalities as soon as possible.
For the automatic feeding system, perform a check and calibration every **7 days**. Also, clean the scale and dirt on the electric heater every **7 days** to prevent excessive internal temperature buildup.
For all water and gas piping systems, conduct checks every **7 days** to identify any leaks or fluid escapes, and promptly repair or replace any faulty pipes.
**3. Maintenance Before Long-Term Shutdown**
If the equipment is scheduled for long-term shutdown, it must be properly maintained to prevent corrosion and aging during the idle period. Actions to take include: clean the floor, removing any water to keep it dry, and ensure the machine platform, tanks, drive systems, and hangers are clean and dry. Wrap all motors in plastic for protection; lubricate all bearings with grease to prevent rust; clean all pipelines thoroughly; and clean the filter barrel and its elements. Lastly, ensure all heaters in the tanks are cleaned to remove any dirt and kept dry.
The electroplating equipment used in printed circuit board production can vary significantly due to different production processes and manufacturers. As a result, maintenance methods may also differ. However, timely and correct maintenance should never be overlooked due to production schedules or output pressures. Only through proper and timely maintenance can the equipment’s normal operation and stable performance be ensured, ultimately safeguarding production quality and output.