1. With the rapid advancement of the electronics industry, printed circuit boards—essential components of electronic products—have experienced significant growth as well.
2. The cover plate and backing plate, serving as auxiliary materials for drilling printed circuit boards, are crucial in optimizing hole quality, minimizing tool wear, extending drill bit lifespan, and enhancing processing efficiency, particularly for high-end PCB products that increasingly rely on these cover backing plates.
3. This article reviews the research surrounding micro-hole drilling technology for the cover plate in PCB micro-hole drilling applications.
4. The criteria for evaluating hole quality include hole position accuracy, burr formation, nail head presence, hole wall roughness, as well as wall staining and tearing.
5. Numerous factors influence the quality of PCB hole processing, such as drilling machine performance, drill bits, and circuit board materials.

and the type and thickness of the cover plate, along with drilling process parameters and the drilling environment. During the PCB drilling process, various boards may encounter distinct challenges, necessitating an examination of the drilling defects associated with each PCB to identify a suitable matching cover plate. Currently, some researchers have begun to explore the drilling characteristics of different types of PCB boards.
(A) Regarding rigid printed circuit boards,
the high hardness of the material presents significant challenges. The drilling temperature and the severe wear on the drill bit are currently the primary issues faced with rigid boards.
(B) In the realm of flexible board drilling,
challenges include difficulties in removing drill cuttings and nail head formation, which adversely affect drilling quality. Wang Sihua and colleagues utilized orthogonal testing to analyze the key factors influencing the drilling quality of flexible boards, finding that the combination of auxiliary materials is critical. Another important factor is the type of copper foil used. Due to the low rigidity of the flexible circuit board material, nail head issues are more likely to occur during the drilling process. For this type of board, it is advisable to choose a phenolic type for the cover and backing plate. Furthermore, research on micro-hole drilling and the drilling quality of flexible printed circuit boards has been conducted.
(3) Concerning rigid-flex boards,
the rigid part is typically made of FR4, while the flexible section is composed of PI or PET. The disparity between these materials can lead to challenges such as inconsistent bonding and varying heat compression shrinkage, making product stability harder to achieve.
Currently, there is limited literature addressing the optimal cover plate combinations for drilling different types of PCB boards. Domestic research remains in its early stages, with only a few industry professionals conducting targeted studies based on practical production needs. Additionally, an analysis of the preparation and performance of glued aluminum substrates for PCB drilling has indicated that these substrates offer better heat absorption and water solubility, potentially lowering the drilling temperature.
Despite these insights, specific effects of the backing plate during the PCB drilling process are infrequently discussed; research on combinations of different PCB drilling cover and backing plates is scarce. Moreover, a comparative analysis of the drilling characteristics across various PCB boards has yet to be developed, highlighting the need for further investigation.
2. The cover plate and backing plate, serving as auxiliary materials for drilling printed circuit boards, are crucial in optimizing hole quality, minimizing tool wear, extending drill bit lifespan, and enhancing processing efficiency, particularly for high-end PCB products that increasingly rely on these cover backing plates.
3. This article reviews the research surrounding micro-hole drilling technology for the cover plate in PCB micro-hole drilling applications.
4. The criteria for evaluating hole quality include hole position accuracy, burr formation, nail head presence, hole wall roughness, as well as wall staining and tearing.
5. Numerous factors influence the quality of PCB hole processing, such as drilling machine performance, drill bits, and circuit board materials.
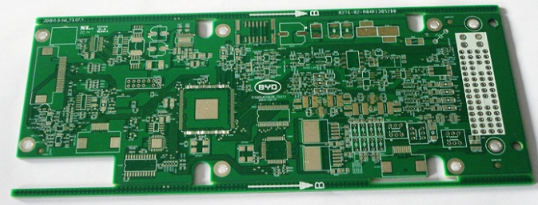
and the type and thickness of the cover plate, along with drilling process parameters and the drilling environment. During the PCB drilling process, various boards may encounter distinct challenges, necessitating an examination of the drilling defects associated with each PCB to identify a suitable matching cover plate. Currently, some researchers have begun to explore the drilling characteristics of different types of PCB boards.
(A) Regarding rigid printed circuit boards,
the high hardness of the material presents significant challenges. The drilling temperature and the severe wear on the drill bit are currently the primary issues faced with rigid boards.
(B) In the realm of flexible board drilling,
challenges include difficulties in removing drill cuttings and nail head formation, which adversely affect drilling quality. Wang Sihua and colleagues utilized orthogonal testing to analyze the key factors influencing the drilling quality of flexible boards, finding that the combination of auxiliary materials is critical. Another important factor is the type of copper foil used. Due to the low rigidity of the flexible circuit board material, nail head issues are more likely to occur during the drilling process. For this type of board, it is advisable to choose a phenolic type for the cover and backing plate. Furthermore, research on micro-hole drilling and the drilling quality of flexible printed circuit boards has been conducted.
(3) Concerning rigid-flex boards,
the rigid part is typically made of FR4, while the flexible section is composed of PI or PET. The disparity between these materials can lead to challenges such as inconsistent bonding and varying heat compression shrinkage, making product stability harder to achieve.
Currently, there is limited literature addressing the optimal cover plate combinations for drilling different types of PCB boards. Domestic research remains in its early stages, with only a few industry professionals conducting targeted studies based on practical production needs. Additionally, an analysis of the preparation and performance of glued aluminum substrates for PCB drilling has indicated that these substrates offer better heat absorption and water solubility, potentially lowering the drilling temperature.
Despite these insights, specific effects of the backing plate during the PCB drilling process are infrequently discussed; research on combinations of different PCB drilling cover and backing plates is scarce. Moreover, a comparative analysis of the drilling characteristics across various PCB boards has yet to be developed, highlighting the need for further investigation.