the automotive electronics market is the third largest application area of PCBs after computers and communications. As automobiles evolve from traditional mechanical products to intelligent, informatized, and mechatronics high-tech products, electronic technology has become ubiquitous in various automotive systems including engine, chassis, security, information, and in-vehicle environmental systems. This widespread integration of electronic components underscores the automotive market’s emergence as a significant segment within the electronics consumer market. Consequently, the advancement of automotive electronics has naturally propelled the development of automotive PCBs.
In today’s key PCB applications, automotive PCBs hold a crucial position. However, due to the unique operating conditions

Given the safety and high current requirements of automotive applications, PCBs face heightened demands for reliability and environmental adaptability. The range of PCB technologies involved is extensive, posing a significant challenge for PCB companies. To successfully penetrate the automotive PCB market, manufacturers must thoroughly understand and analyze its unique requirements.
Automotive PCBs prioritize high reliability and low DPPM (defective parts per million). Does our company possess the requisite technology and experience for high-reliability manufacturing? Is this aligned with our future product development goals? Can we effectively meet TS16949 process control standards and achieve low DPPM rates? These critical questions demand careful evaluation. Pursuing this lucrative market blindly can prove detrimental to the enterprise.
Below are some notable practices in the testing processes of leading companies specialized in automotive PCB production, offered for the reference of PCB professionals:
1. **Secondary Testing Method:**
Some manufacturers employ a “secondary testing method” to enhance detection rates of faulty boards post initial high-voltage electrical stress testing.
2. **Bad Board Foolproof Testing System:**
Increasingly, manufacturers integrate “good board marking systems” and “bad board error prevention boxes” into light board testing machines to prevent human errors effectively. The good board marking system identifies PASS boards, ensuring they do not mistakenly reach customers. The bad board error prevention box signals operators during testing: it opens for PASS boards and closes for defective boards, ensuring correct handling.
Creating Gerber files for PCB designs can sometimes be challenging in accurately reflecting the desired product. Advanced Circuits offers valuable tips to mitigate common design errors that may delay PCB orders and impact turnaround times. Designers often overlook crucial details such as aperture lists, drill files, drill lists, or fail to meet complete manufacturing requirements.
Utilizing Advanced Circuits’ FreeDFM system simplifies the design and submission process. It integrates seamlessly to identify potential DFM issues, enabling corrections prior to submission. This unified approach ensures that PCB designs meet rigorous manufacturing standards and facilitates a smoother manufacturing process under professional oversight.
In today’s key PCB applications, automotive PCBs hold a crucial position. However, due to the unique operating conditions
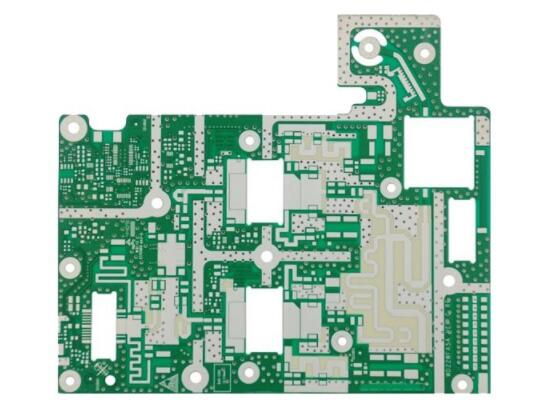
Given the safety and high current requirements of automotive applications, PCBs face heightened demands for reliability and environmental adaptability. The range of PCB technologies involved is extensive, posing a significant challenge for PCB companies. To successfully penetrate the automotive PCB market, manufacturers must thoroughly understand and analyze its unique requirements.
Automotive PCBs prioritize high reliability and low DPPM (defective parts per million). Does our company possess the requisite technology and experience for high-reliability manufacturing? Is this aligned with our future product development goals? Can we effectively meet TS16949 process control standards and achieve low DPPM rates? These critical questions demand careful evaluation. Pursuing this lucrative market blindly can prove detrimental to the enterprise.
Below are some notable practices in the testing processes of leading companies specialized in automotive PCB production, offered for the reference of PCB professionals:
1. **Secondary Testing Method:**
Some manufacturers employ a “secondary testing method” to enhance detection rates of faulty boards post initial high-voltage electrical stress testing.
2. **Bad Board Foolproof Testing System:**
Increasingly, manufacturers integrate “good board marking systems” and “bad board error prevention boxes” into light board testing machines to prevent human errors effectively. The good board marking system identifies PASS boards, ensuring they do not mistakenly reach customers. The bad board error prevention box signals operators during testing: it opens for PASS boards and closes for defective boards, ensuring correct handling.
Creating Gerber files for PCB designs can sometimes be challenging in accurately reflecting the desired product. Advanced Circuits offers valuable tips to mitigate common design errors that may delay PCB orders and impact turnaround times. Designers often overlook crucial details such as aperture lists, drill files, drill lists, or fail to meet complete manufacturing requirements.
Utilizing Advanced Circuits’ FreeDFM system simplifies the design and submission process. It integrates seamlessly to identify potential DFM issues, enabling corrections prior to submission. This unified approach ensures that PCB designs meet rigorous manufacturing standards and facilitates a smoother manufacturing process under professional oversight.