**Introduction to PCB Vias**
Vias are integral components in printed circuit board (PCB) design, playing a crucial role in ensuring electrical connections, component placement, and stability. A via consists of three main elements: the hole, the surrounding pad area, and the power layer isolation area.
**Via Structure and Functionality**
The via hole itself is a cylindrical opening that enables electrical continuity between different layers of the PCB. A metal layer is electroplated onto the walls of the via hole, ensuring a conductive path that connects the copper traces of the various inner layers of the PCB. The via’s upper and lower openings are typically designed with pads—circular areas of copper that allow for either direct connection of signals or, in some cases, isolation.
The design of vias is a critical aspect of multi-layer PCB manufacturing. The pad areas on both sides of the via hole are used to connect traces on the top and bottom layers or between internal layers, facilitating the transfer of electrical signals throughout the board. The power layer isolation zone helps prevent short circuits and ensures proper signal integrity across the PCB.
**Conclusion**
In summary, vias serve as the backbone of interlayer communication in PCBs. Proper via design is essential for ensuring the reliable performance of multi-layer PCBs, as it guarantees secure electrical connections and optimized component placement across all layers.

### Types of Vias in PCB Design
In printed circuit board (PCB) design, vias are essential for establishing connections between different layers of the board. These vias are typically categorized into three main types: blind vias, buried vias, and through holes.
1. **Blind Vias**: These vias connect the surface layers of the PCB to one or more inner layers, but they do not extend through the entire board. Blind vias have a specific depth, with the aperture and hole depth being in a certain ratio to ensure reliable connections between the surface and inner circuits.
2. **Buried Vias**: These vias are located entirely within the inner layers of the PCB. They do not appear on the board’s surface and are used to connect the inner layers. Since they are not visible from the outside, buried vias are typically used for more complex multi-layer PCB designs.
3. **Through Holes**: These vias pass through the entire PCB from the top to the bottom layers. Through holes are commonly used for component mounting and alignment. They are also employed for connecting all layers of the PCB, especially when signal or power continuity is needed across the board.
### Via Design in Typical PCB Layouts
In general PCB designs, the impact of parasitic capacitance and inductance from vias is minimal. For a typical 1- to 4-layer PCB, a via design with a 0.36mm aperture, 0.61mm pad size, and a 1.02mm POWER isolation area is commonly used. For special signal lines, such as power or ground traces, vias with slightly larger dimensions, such as 0.41mm aperture, 0.81mm pad, and 1.32mm POWER isolation area, are typically selected to accommodate higher current demands.
### Reasons for Unconnected Vias in PCB Manufacturing
Several issues can lead to unconnected or defective vias in a PCB. These issues often arise during the drilling, plating, or soldering stages.
1. **Drilling Defects**
PCB boards are made from epoxy resin and fiberglass, and when drilling vias, residual dust or debris may remain inside the holes if not properly cleaned. If the debris is not removed, the vias will fail to sink copper during the plating process, resulting in an incomplete or non-functional via connection. These defects are often detected during the flying probe test.
2. **Heavy Copper Plating Issues**
When copper plating is done too quickly or improperly, the copper inside the via may not fully fill the hole. This results in weak or incomplete copper connections, which can cause operational issues. Problems in the copper deposition process, such as incomplete development, over-etching, or insufficient cleaning of residual chemicals, can lead to these defects.
3. **Excessive Current Demand for Via Copper**
In certain cases, the vias may need to handle higher currents than originally specified. If the copper in the via is not thickened to accommodate the increased current, the excessive heat can cause the via copper to melt or become damaged, leading to a failure in the connection.
4. **Soldering Defects in SMT**
During surface-mount technology (SMT) soldering, the vias may be exposed to prolonged heating if the components are left in the soldering furnace too long. Excessive heat can cause the copper in the via to melt, resulting in defects such as broken or disconnected vias. These issues are typically related to poor soldering process control or incorrect temperature settings.
### Teardrop Patching in PCB Design
Teardrop patching is a technique used to enhance the mechanical integrity of the PCB, particularly at the junctions where copper traces meet pads or vias. The goal of teardrop patching is to prevent damage to the copper traces during mechanical drilling. This technique involves gradually widening the copper trace where it connects to the pad or via, forming a shape similar to a teardrop. This gradual transition helps reduce stress concentrations and the likelihood of trace or via failure during the manufacturing process.
By applying teardrop patching, the risk of damaging the copper traces is minimized, leading to more reliable and robust PCB designs.

**The Importance of Teardrop Filling in PCB Design**
To prevent pad or via damage during the drilling process when manufacturing a mechanical PCB, it is crucial to ensure that the connection between the copper traces and pads or vias is adequately reinforced. This can be achieved by widening the copper traces at the connection point, reducing the likelihood of failure under drilling pressure. Additionally, filling the joint with a teardrop shape smoothens the connection, reducing the risk of copper wire corrosion from residual chemicals used during the manufacturing process.
**1. Preventing Disconnection and Enhancing Aesthetics**
Teardrop filling plays a vital role in preventing disconnection between the trace and the pad or via, especially under significant external mechanical stress. This helps maintain the integrity of the PCB design and ensures that the connections remain intact. Furthermore, the teardrop shape contributes to a more visually appealing design, improving the overall aesthetics of the PCB.
**2. Protecting Pads During Soldering**
When soldering, teardrop filling offers protection to the pads, reducing the likelihood of pad detachment after multiple soldering cycles. This feature is particularly useful in maintaining the long-term reliability of the PCB, preventing damage from repeated thermal cycles and mechanical stress during assembly.
**3. Preventing Production Issues**
In the production phase, teardrop filling helps mitigate potential problems such as uneven etching or cracks caused by via misalignment. This technique enhances the overall quality of the PCB by reducing the risk of manufacturing defects that can lead to failures in the finished product.
**4. Improving Signal Integrity**
Teardrop filling smoothens impedance transitions, crucial for high-frequency signal transmission. It reduces abrupt impedance changes and minimizes signal reflection caused by sudden decreases in trace width. By ensuring smoother connections between traces and component pads, teardrop filling helps maintain signal integrity, especially in high-speed and high-frequency applications. This results in a more reliable PCB performance, particularly in sensitive electronic devices.
In conclusion, incorporating teardrop filling in PCB design is a valuable technique that improves the mechanical, aesthetic, and electrical performance of the board. It ensures the robustness of connections, protects the integrity of pads, and enhances signal transmission efficiency.
Vias are integral components in printed circuit board (PCB) design, playing a crucial role in ensuring electrical connections, component placement, and stability. A via consists of three main elements: the hole, the surrounding pad area, and the power layer isolation area.
**Via Structure and Functionality**
The via hole itself is a cylindrical opening that enables electrical continuity between different layers of the PCB. A metal layer is electroplated onto the walls of the via hole, ensuring a conductive path that connects the copper traces of the various inner layers of the PCB. The via’s upper and lower openings are typically designed with pads—circular areas of copper that allow for either direct connection of signals or, in some cases, isolation.
The design of vias is a critical aspect of multi-layer PCB manufacturing. The pad areas on both sides of the via hole are used to connect traces on the top and bottom layers or between internal layers, facilitating the transfer of electrical signals throughout the board. The power layer isolation zone helps prevent short circuits and ensures proper signal integrity across the PCB.
**Conclusion**
In summary, vias serve as the backbone of interlayer communication in PCBs. Proper via design is essential for ensuring the reliable performance of multi-layer PCBs, as it guarantees secure electrical connections and optimized component placement across all layers.
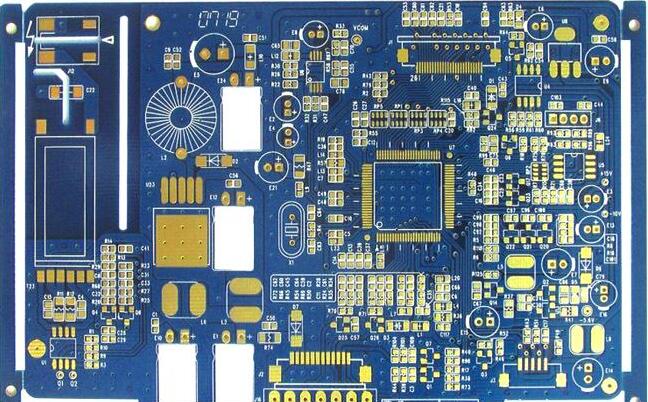
### Types of Vias in PCB Design
In printed circuit board (PCB) design, vias are essential for establishing connections between different layers of the board. These vias are typically categorized into three main types: blind vias, buried vias, and through holes.
1. **Blind Vias**: These vias connect the surface layers of the PCB to one or more inner layers, but they do not extend through the entire board. Blind vias have a specific depth, with the aperture and hole depth being in a certain ratio to ensure reliable connections between the surface and inner circuits.
2. **Buried Vias**: These vias are located entirely within the inner layers of the PCB. They do not appear on the board’s surface and are used to connect the inner layers. Since they are not visible from the outside, buried vias are typically used for more complex multi-layer PCB designs.
3. **Through Holes**: These vias pass through the entire PCB from the top to the bottom layers. Through holes are commonly used for component mounting and alignment. They are also employed for connecting all layers of the PCB, especially when signal or power continuity is needed across the board.
### Via Design in Typical PCB Layouts
In general PCB designs, the impact of parasitic capacitance and inductance from vias is minimal. For a typical 1- to 4-layer PCB, a via design with a 0.36mm aperture, 0.61mm pad size, and a 1.02mm POWER isolation area is commonly used. For special signal lines, such as power or ground traces, vias with slightly larger dimensions, such as 0.41mm aperture, 0.81mm pad, and 1.32mm POWER isolation area, are typically selected to accommodate higher current demands.
### Reasons for Unconnected Vias in PCB Manufacturing
Several issues can lead to unconnected or defective vias in a PCB. These issues often arise during the drilling, plating, or soldering stages.
1. **Drilling Defects**
PCB boards are made from epoxy resin and fiberglass, and when drilling vias, residual dust or debris may remain inside the holes if not properly cleaned. If the debris is not removed, the vias will fail to sink copper during the plating process, resulting in an incomplete or non-functional via connection. These defects are often detected during the flying probe test.
2. **Heavy Copper Plating Issues**
When copper plating is done too quickly or improperly, the copper inside the via may not fully fill the hole. This results in weak or incomplete copper connections, which can cause operational issues. Problems in the copper deposition process, such as incomplete development, over-etching, or insufficient cleaning of residual chemicals, can lead to these defects.
3. **Excessive Current Demand for Via Copper**
In certain cases, the vias may need to handle higher currents than originally specified. If the copper in the via is not thickened to accommodate the increased current, the excessive heat can cause the via copper to melt or become damaged, leading to a failure in the connection.
4. **Soldering Defects in SMT**
During surface-mount technology (SMT) soldering, the vias may be exposed to prolonged heating if the components are left in the soldering furnace too long. Excessive heat can cause the copper in the via to melt, resulting in defects such as broken or disconnected vias. These issues are typically related to poor soldering process control or incorrect temperature settings.
### Teardrop Patching in PCB Design
Teardrop patching is a technique used to enhance the mechanical integrity of the PCB, particularly at the junctions where copper traces meet pads or vias. The goal of teardrop patching is to prevent damage to the copper traces during mechanical drilling. This technique involves gradually widening the copper trace where it connects to the pad or via, forming a shape similar to a teardrop. This gradual transition helps reduce stress concentrations and the likelihood of trace or via failure during the manufacturing process.
By applying teardrop patching, the risk of damaging the copper traces is minimized, leading to more reliable and robust PCB designs.
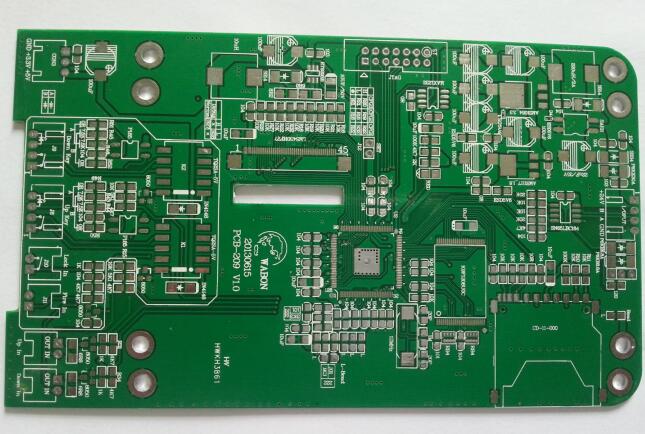
**The Importance of Teardrop Filling in PCB Design**
To prevent pad or via damage during the drilling process when manufacturing a mechanical PCB, it is crucial to ensure that the connection between the copper traces and pads or vias is adequately reinforced. This can be achieved by widening the copper traces at the connection point, reducing the likelihood of failure under drilling pressure. Additionally, filling the joint with a teardrop shape smoothens the connection, reducing the risk of copper wire corrosion from residual chemicals used during the manufacturing process.
**1. Preventing Disconnection and Enhancing Aesthetics**
Teardrop filling plays a vital role in preventing disconnection between the trace and the pad or via, especially under significant external mechanical stress. This helps maintain the integrity of the PCB design and ensures that the connections remain intact. Furthermore, the teardrop shape contributes to a more visually appealing design, improving the overall aesthetics of the PCB.
**2. Protecting Pads During Soldering**
When soldering, teardrop filling offers protection to the pads, reducing the likelihood of pad detachment after multiple soldering cycles. This feature is particularly useful in maintaining the long-term reliability of the PCB, preventing damage from repeated thermal cycles and mechanical stress during assembly.
**3. Preventing Production Issues**
In the production phase, teardrop filling helps mitigate potential problems such as uneven etching or cracks caused by via misalignment. This technique enhances the overall quality of the PCB by reducing the risk of manufacturing defects that can lead to failures in the finished product.
**4. Improving Signal Integrity**
Teardrop filling smoothens impedance transitions, crucial for high-frequency signal transmission. It reduces abrupt impedance changes and minimizes signal reflection caused by sudden decreases in trace width. By ensuring smoother connections between traces and component pads, teardrop filling helps maintain signal integrity, especially in high-speed and high-frequency applications. This results in a more reliable PCB performance, particularly in sensitive electronic devices.
In conclusion, incorporating teardrop filling in PCB design is a valuable technique that improves the mechanical, aesthetic, and electrical performance of the board. It ensures the robustness of connections, protects the integrity of pads, and enhances signal transmission efficiency.