1. Mobile phones, computers, tablets, and other electronic devices are an indispensable part of modern life. Have you ever wondered how these electronic devices are manufactured?
2. Next, we will introduce a technology used in the production of all electronic devices: surface-mount technology (SMT).
3. In simple terms, SMT involves printing solder paste onto designated spots on a PCB circuit board. Resistors, capacitors, and other components are then placed on the surface of the circuit board using machinery. The board is then baked at high temperatures to cure the solder paste, which securely attaches the components to the board, resulting in a complete circuit board assembly.
4. The SMT production line primarily consists of the following equipment: solder paste printer, solder paste inspection equipment (SPI), placement machine, Automated Optical Inspection (AOI), reflow oven, board loaders and unloaders, rework station, and other associated equipment.

1. Among them, solder paste printers, placement machines, and reflow ovens are categorized as processing equipment, while SPI and AOI are classified as inspection equipment. The upper and lower board machines, connection equipment, rework stations, and other auxiliary tools also play essential roles.
2. Typically, an SMT production line is arranged in the sequence of upper board machine – solder paste printer – solder paste inspection equipment (SPI) – placement machine – front AOI – reflow oven – back AOI – rework station – lower board machine, with single-track or double-track transmission and connection equipment interspersed throughout.
3. Solder paste printer: Applies solder paste onto a stencil, using a robotic arm to control the scraper, which moves the solder paste from one end of the stencil to the other. The solder paste then leaks through the stencil holes and deposits onto the corresponding positions on the PCB board below.
4. Solder Paste Inspection Equipment (SPI): Uses optical principles to assess the quality of solder paste after printing, detecting issues such as missing paste, insufficient or excessive solder, bridging, misalignment, poor shape, and contamination of the board surface.
5. Mounter: Utilizes a suction nozzle to pick up components and place them onto the PCB surface at the correct positions, controlled by a mechanical arm.
6. AOI: Performs optical inspection of component placement to check for displacement, missing components, polarity issues, skew, incorrect parts, and other defects. After reflow soldering, it also detects problems like insufficient or excess solder, misalignment, and poor soldering quality.
7. Reflow oven: Features various temperature zones heated by hot air or infrared radiation, creating a gradient temperature profile. As the PCB board moves through the oven, the solder paste solidifies due to the increasing temperature.
8. Board loading and unloading machine, connection equipment: Equipment used to transfer PCB boards.
9. Rework station: Provides heating capabilities and is used for manual inspection and repair of PCBs that have been reworked and soldered.
10. The application of SMT is widespread. For instance, the smartphones everyone uses today are made from circuit boards produced through this process. These boards are then assembled with cameras, thermal conductive adhesives, screens, and other materials into complete phones. Companies such as Foxconn, Huawei, OPPO, VIVO, Xiaomi, BYD, and others operate their own SMT lines, with major electronics manufacturers like Foxconn serving as notable foundries, such as for Apple.
11. Despite the maturity of current SMT technology, several challenges persist:
– The accuracy of equipment cannot achieve 100%, and errors can still lead to the scrapping of soldered PCBs.
– Manual intervention is necessary for verification and repair.
– Complex and precise parts face aging and damage risks, potentially causing production line shutdowns.
– Equipment data platforms from different manufacturers lack compatibility.
12. Therefore, the future development trend for SMT production lines is clear:
– Devices will incorporate closed-loop detection, utilizing in-depth learning and self-evolution through error processing to ensure correct performance in similar situations in the future.
– There will be complete interconnectivity among equipment platforms, compatible with the enterprise’s MES system, allowing one server to manage multiple lines simultaneously, adjusting production capacity and material transport in real-time based on data.
– Core equipment components will be monitored, such as adding a monitoring system to the hot air motor of the reflow oven to track real-time motor performance and enable timely manual intervention if anomalies occur.
– Equipment will feature early warning and foolproof functions. Since electronic equipment cannot guarantee immunity to issues like line aging or short circuits, smart devices will include instant alarms and automatic power-off features to ensure safety and prevent production hazards.
– Unmanned management will be fully realized, with industrial robots and intelligent robots performing repairs, inspections, and other tasks, allowing a minimal number of human operators to oversee an entire SMT factory.
2. Next, we will introduce a technology used in the production of all electronic devices: surface-mount technology (SMT).
3. In simple terms, SMT involves printing solder paste onto designated spots on a PCB circuit board. Resistors, capacitors, and other components are then placed on the surface of the circuit board using machinery. The board is then baked at high temperatures to cure the solder paste, which securely attaches the components to the board, resulting in a complete circuit board assembly.
4. The SMT production line primarily consists of the following equipment: solder paste printer, solder paste inspection equipment (SPI), placement machine, Automated Optical Inspection (AOI), reflow oven, board loaders and unloaders, rework station, and other associated equipment.
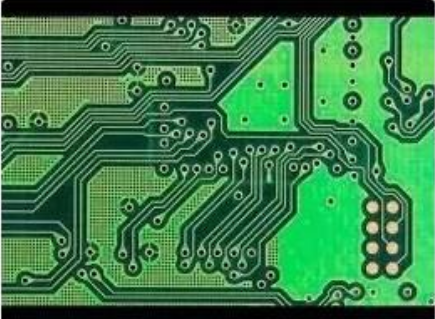
1. Among them, solder paste printers, placement machines, and reflow ovens are categorized as processing equipment, while SPI and AOI are classified as inspection equipment. The upper and lower board machines, connection equipment, rework stations, and other auxiliary tools also play essential roles.
2. Typically, an SMT production line is arranged in the sequence of upper board machine – solder paste printer – solder paste inspection equipment (SPI) – placement machine – front AOI – reflow oven – back AOI – rework station – lower board machine, with single-track or double-track transmission and connection equipment interspersed throughout.
3. Solder paste printer: Applies solder paste onto a stencil, using a robotic arm to control the scraper, which moves the solder paste from one end of the stencil to the other. The solder paste then leaks through the stencil holes and deposits onto the corresponding positions on the PCB board below.
4. Solder Paste Inspection Equipment (SPI): Uses optical principles to assess the quality of solder paste after printing, detecting issues such as missing paste, insufficient or excessive solder, bridging, misalignment, poor shape, and contamination of the board surface.
5. Mounter: Utilizes a suction nozzle to pick up components and place them onto the PCB surface at the correct positions, controlled by a mechanical arm.
6. AOI: Performs optical inspection of component placement to check for displacement, missing components, polarity issues, skew, incorrect parts, and other defects. After reflow soldering, it also detects problems like insufficient or excess solder, misalignment, and poor soldering quality.
7. Reflow oven: Features various temperature zones heated by hot air or infrared radiation, creating a gradient temperature profile. As the PCB board moves through the oven, the solder paste solidifies due to the increasing temperature.
8. Board loading and unloading machine, connection equipment: Equipment used to transfer PCB boards.
9. Rework station: Provides heating capabilities and is used for manual inspection and repair of PCBs that have been reworked and soldered.
10. The application of SMT is widespread. For instance, the smartphones everyone uses today are made from circuit boards produced through this process. These boards are then assembled with cameras, thermal conductive adhesives, screens, and other materials into complete phones. Companies such as Foxconn, Huawei, OPPO, VIVO, Xiaomi, BYD, and others operate their own SMT lines, with major electronics manufacturers like Foxconn serving as notable foundries, such as for Apple.
11. Despite the maturity of current SMT technology, several challenges persist:
– The accuracy of equipment cannot achieve 100%, and errors can still lead to the scrapping of soldered PCBs.
– Manual intervention is necessary for verification and repair.
– Complex and precise parts face aging and damage risks, potentially causing production line shutdowns.
– Equipment data platforms from different manufacturers lack compatibility.
12. Therefore, the future development trend for SMT production lines is clear:
– Devices will incorporate closed-loop detection, utilizing in-depth learning and self-evolution through error processing to ensure correct performance in similar situations in the future.
– There will be complete interconnectivity among equipment platforms, compatible with the enterprise’s MES system, allowing one server to manage multiple lines simultaneously, adjusting production capacity and material transport in real-time based on data.
– Core equipment components will be monitored, such as adding a monitoring system to the hot air motor of the reflow oven to track real-time motor performance and enable timely manual intervention if anomalies occur.
– Equipment will feature early warning and foolproof functions. Since electronic equipment cannot guarantee immunity to issues like line aging or short circuits, smart devices will include instant alarms and automatic power-off features to ensure safety and prevent production hazards.
– Unmanned management will be fully realized, with industrial robots and intelligent robots performing repairs, inspections, and other tasks, allowing a minimal number of human operators to oversee an entire SMT factory.