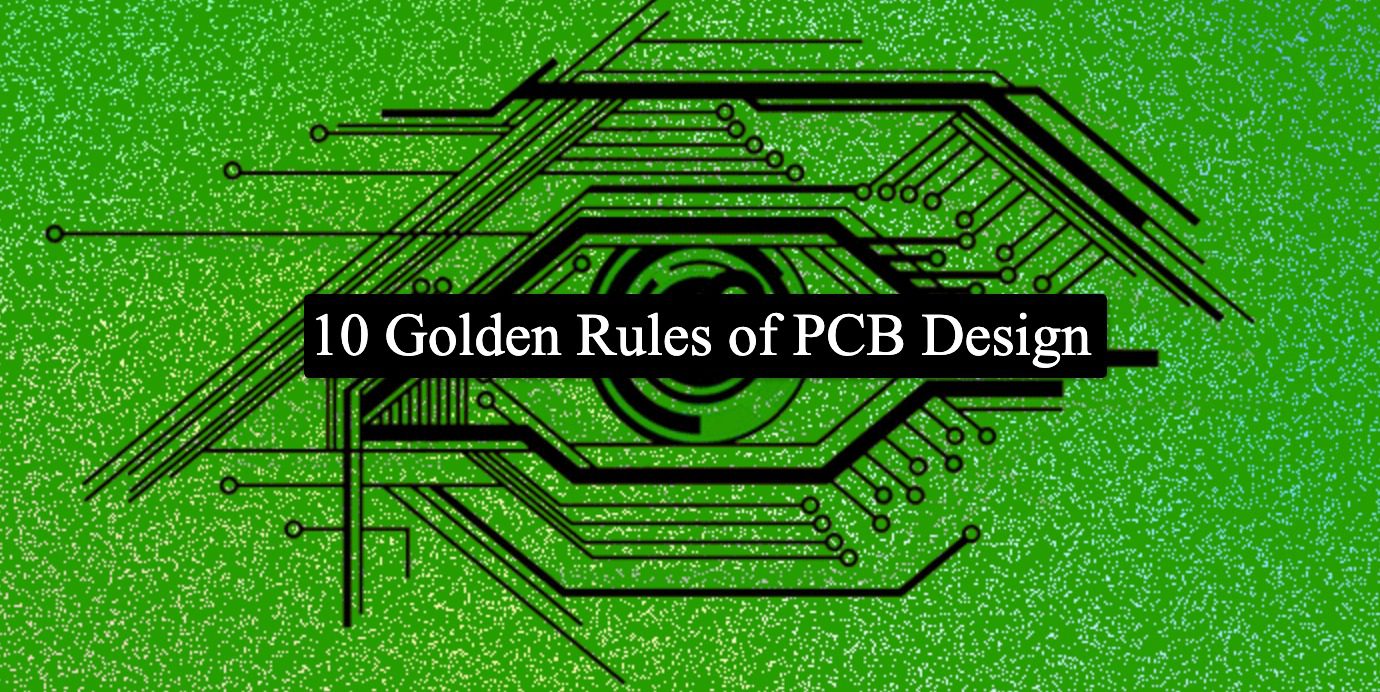
Ten Golden Rules of PCB Design
A PCB or Print Circuit Board is one of the most fundamental components of any electronic device. It is the support system for most flexible and bendy electronic parts. It carries all the elements that combine to make a final circuit board. The actual function of a PCB is to connect the electronic components with the software and the peripheral hardware to produce a new product. The PCBs are the most crucial components of any electronic device. Thus, their assembly and production need to be accurate and rigid.
However, as the electronics field maximizes daily, new innovations have created newer designs to assemble a PCB, but many applications still need to use a custom PCB.
Why do we need a PCB design guideline?
A PCB design guideline will reduce the cost of repeated manufacturing because, considering the human factors, some errors while assembling the various components of the PCB circuit board might arise if the verification and rectification are not on the prototype. Thus, it is always advisable to first create a prototype and run test trial on them to ensure maximum functionality of your PCB design.
This article will introduce 10 golden rules that electronics and communications engineers should consider when using any PCB design software. However, the common PCB design rules have been fundamentally the same for decades and are used widely in many PCB design projects.
Still, this article intends to throw light on some PCB design rules and PCB design guidelines.
Rules for PCB Design –
Although everyone has their own ideas behind a PCB design, moreover, it depends on the type of component in which the PCB has to be fit. Still, here is a list of some common PCB design guidelines that one must follow before starting any PCB design project –
- Choose the right grid set: When you start designing a PCB, you must choose the type of grid whose spacing is in tune with most of the components of a PCB. Choosing the correct grid size helps you eliminate complicated circuit connections and ensures optimum circuit board applications. Moreover, since every device is of a different size, every grid has to be different. So, while you prepare a PCB design, you must remember that you are using the correct-sized grid, which is favorable to the design. If you are using a multi-grid circuit board, then the polygon is very important for circuit board copper.
- Short and Direct Path: While you make connections in the circuit board while designing a PCB, keep the wiring short and direct. The wiring should be kept short and direct during all the stages to ensure maximum track length. The short and direct paths are suitable for high-speed digital circuits so that their performance doesn’t get restricted by impedance.
- Use Power Layer: While you go for any PCB design project, you must remember to use a copper-coated power layer to connect the multiple wirings. Minimum voltage loss, good current efficiency, and a suitable grounding return line are all ensured by this wire design. All this can be done if you ensure using a copper-coated power layer to make connections in your PCB design.
- Use reasonable directions: Whether the current is AC or DC, ensure that your PCB design has a reasonable direction. Regardless of the AC or DC current, high or low frequency, weak or strong signals, input or output, or high/low voltage, the PCB design project has to have reasonable directions. Experts recommend using a straight direction rather than a ring or other intertwined wiring direction. This helps eliminate any interferences or impediments. Also, make sure you group all the related components with the required test points attached to each one of the components. This will ease the process of testing the PCB after the engineer has designed it.
- Design the rule-check: After the PCB design project is complete and the wirings are done, ensure a physical check. Physically verifying the schematic is a worthwhile technique. Complex design settings benefit even more from running the DRC function test. You should therefore carry out a large number of DRC tests in order to ensure the accuracy of your routing decisions.
- Screen Printing: Circuit board makers, engineers, installers, and commissioning people to benefit from screen printing, which marks different points (functional and test), connector or component orientation, and other important information. It streamlines the manufacturing process and reduces the potential for errors to a minimum. By using screen printing on both upper and bottom surfaces or circuit board components, production processes can be streamlined.
- Copy the circuit board: Copy the PCB circuit board you designed on a large circuit board. For a manufacturer, it is crucial to choose the most suitable size for the equipment to cut the cost of prototyping. You must carry out the circuit board layout on a panel, make each panel size-specific to obtain the required size of the PCB, and then modify it as per the requirements. If you do not get the correct size, repeat the whole exercise multiple times within these panel sizes to obtain your desired PCB size.
- Integrate the component Values: If you are involved in a PCB design project, you must choose discrete components with higher or lower component values as required. This integration can simplify the cost of bills and reduce the manufacturing cost. Moreover, if you have to design a series of PCBs, this integration will help you to make the correct inventory management decision from a longer-term perspective.
- Decoupling Capacitance: One of the most important PCB design guidelines is not to optimize your design by ignoring the over coupling of the power lines based on the limit values. Designers should not rely solely on component datasheet restrictions, and they should steer clear of power cord connection at all costs. However, you can take as much time as you need to assemble the capacitors because capacitors come at low costs and are capable of durable performance.
- Generate and verify the PCB coupling parameters: Once the PCB design is ready, you must develop and confirm all the parameters before you forward it further for production. This will eliminate misinterpretations and ensure the expected output. If there are any inadvertent blunders or loose connections, you will be able to detect them at this stage, thus avoiding manufacturing the products with the wrong parameters. Most PCB design project managers verify the design themselves rather than forwarding it to a team for verification. When you verify the circuit yourself, you might be able to detect and eliminate all possible errors and prevent the production of an incorrectly configured PCB.
Conclusion
Thoroughly following the PCB design rules negates the possibility of any errors in designing. Another advantage of going through the PCB design guidelines is the production of a safe and high-performing product. This will optimize the use of your PCB more effectively. Many PCB manufacturing companies do the verification and rectification for you. A good manufacturer can be your trusted electronic assembly partner. This will reduce your cost of manufacturing incorrect circuit boards. If you have a dedicated team of PCB designers, you can approach them for this verification and testing. Regardless of the size of your project, these companies can take your product from concept to production with ease.