Flexible Printed Circuit Boards (Flex PCBs) are revolutionizing electronics with their dynamic, bendable designs. As devices shrink and demand for high-performance, compact solutions surges, understanding Flex PCB technology is critical for engineers and manufacturers.
What Are Flexible PCBs?
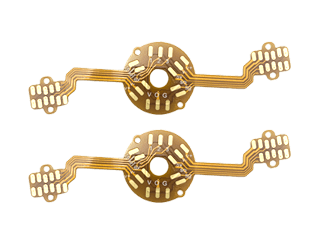
Flexible PCBs are circuit boards made from polyimide or other flexible polymer substrates, enabling them to bend, twist, and conform to complex shapes. Unlike rigid PCBs (built with fiberglass), their lightweight, thin-profile design supports advanced applications like foldable smartphones, wearables, and automotive sensors23.
Key Advantages Over Rigid PCBs
- Space Optimization: Ideal for compact devices (e.g., IoT sensors, medical implants), reducing assembly size by up to 60%2.
- Enhanced Durability: Withstand vibrations and mechanical stress, critical for aerospace and automotive systems2.
- Heat Dissipation: Polyimide materials efficiently manage thermal loads in high-power microdevices3.
- Weight Reduction: Up to 70% lighter than rigid boards, crucial for drones and satellites2.
Types of Flexible PCBs: IPC Classifications & Innovations
Flex PCBs are categorized under IPC-6013 standards, with three primary types:
Type | Structure | Applications |
---|---|---|
Type 1 (Single-Sided) | Single conductive layer | Simple circuits (LED strips, calculators) |
Type 2 (Double-Sided) | Dual conductive layers | Wearables, automotive dashboards |
Type 3 (Multilayer) | 3+ conductive layers | 5G基站, military radar systems |
2025 Trends:
- Stiffener Integration: Hybrid designs combine flexible and rigid sections (Rigid-Flex PCBs) for high-density interconnects in robotics23.
- HDI Flex Circuits: Microvias and ultra-thin traces (<25µm) enable miniaturization for AR/VR headsets2.
- Eco-Friendly Materials: Bio-based polyimide reduces environmental impact, aligning with global sustainability mandates1.
Cutting-Edge Applications Driving Market Growth
1. Automotive Electronics
Flex PCBs power ADAS sensors, EV battery monitors, and in-cabin displays. The shift to autonomous vehicles is projected to boost demand by 22% CAGR through 20301.
2. Medical Devices
Biocompatible flex circuits enable implantable glucose monitors and endoscopic cameras, with the medical PCB market expected to reach $4.8B by 20271.
3. 5G & Wearable Technology
Ultra-thin antennas and foldable smartphone hinges rely on Flex PCBs. The 5G infrastructure market alone will require 12M+ flex circuits annually by 202612.
Design Best Practices for High-Yield Flex PCB Manufacturing
- Material Selection: Use adhesiveless laminates (e.g., DuPont Pyralux) to prevent delamination during bending2.
- Dynamic Flex Zones: Limit bend radius to >10x substrate thickness for longevity3.
- Thermal Management: Embed copper pours in multilayer designs to dissipate heat from GaN/SiC components2.
- Testing Protocols: Implement automated optical inspection (AOI) and impedance control for aerospace-grade reliability2.
Future Outlook: Why Flex PCBs Dominate Next-Gen Tech
With the global Flex PCB market projected to hit $27B by 2030, advancements in stretchable electronics and AI-driven design tools will unlock breakthroughs in soft robotics and smart textiles1.
Partner with Experts: Whether developing Rigid-Flex prototypes or scaling production, collaborate with ISO-certified manufacturers to leverage DFM insights and cost-saving strategies2.
Optimize your next project—Explore our PCB manufacturing guide or contact our team for tailored solutions.
Keywords: Flexible PCBs, Rigid-Flex PCB Design, Polyimide Substrates, 5G Technology, Automotive Electronics, IPC-6013 Standards.