**What Are the PCBA Test Methods?**
The process flow of PCBA (Printed Circuit Board Assembly) manufacturing is intricate and involves several crucial steps, such as PCB fabrication, component sourcing and inspection, SMT assembly, DIP insertion, and PCBA testing. Among these stages, PCBA testing is the most critical quality control phase, as it determines the final functionality and reliability of the product. So, what are the primary PCBA test methods?
PCBA testing encompasses five main types: ICT (In-Circuit Test), FCT (Functional Test), aging test, fatigue test, and testing under harsh environmental conditions. Here is an overview of each:
1. **ICT Test**
The ICT test primarily focuses on electrical checks, including continuity testing, voltage and current measurement, fluctuation analysis, amplitude checks, and noise detection. This step ensures that there are no electrical faults such as short circuits or open circuits, which could affect the board’s performance.
2. **FCT Test**
FCT involves functional testing by firing the IC program and simulating the entire PCBA’s functionality. It identifies issues in both hardware and software. This test requires the use of production fixtures and test racks to emulate real-world operating conditions and confirm that the PCBA works as intended.
3. **Aging Test**
The aging test involves subjecting a sample of PCBA boards to extended, high-frequency operational stress. This process is designed to simulate long-term usage and observe any failures or performance degradation over time. The results help assess the product’s longevity and predict failure probabilities under normal operating conditions.
4. **Fatigue Test**
In the fatigue test, PCBA boards undergo repeated or cyclic stress to simulate the wear and tear that can occur during normal operation. The goal is to evaluate the durability of the PCBA components over an extended period, identifying any potential weaknesses that may cause failures under prolonged usage.
5. **Harsh Environment Test**
This test exposes PCBA boards to extreme conditions such as high or low temperatures, high humidity, drops, splashes, and vibrations. By evaluating random samples under these stressful conditions, this test provides insights into the overall reliability and robustness of the entire batch of PCBA boards, predicting how the product will perform in demanding environments.
In conclusion, these five PCBA testing methods are essential for ensuring the quality and reliability of the final product. Each method serves a specific purpose, collectively providing a comprehensive assessment of the PCBA’s performance in both normal and extreme conditions.

The aging test is primarily conducted by continuously powering the PCBA board and electronic products for an extended period. This process ensures that the products remain operational, allowing any potential failures or issues to be observed. After the aging test is completed successfully, the electronic products are considered ready for mass production and sale.
In this article, I will introduce the various PCBA testing methods. The PCBA manufacturing process is intricate, and during production, various issues can arise due to improper equipment or operational errors. As a result, there is no guarantee that all products will meet the required quality standards. To ensure that each product is free of defects, PCB testing is essential.
As environmental protection standards continue to rise and regulations become more stringent, PCB manufacturers face both challenges and opportunities. If these manufacturers can successfully address environmental concerns, particularly pollution, they will position themselves at the forefront of the market. This creates potential for growth and further development in the industry, especially for FPC (flexible printed circuit) products.
The rise of the internet has significantly transformed traditional marketing methods. By leveraging the internet, resources are consolidated on a larger scale, accelerating the development of FPC flexible circuit boards. As development accelerates, PCB manufacturers must also address the environmental challenges that arise from this rapid expansion. However, the internet’s growth has also brought significant advancements in environmental protection and information technology. Data centers dedicated to environmental monitoring and the concept of green electronics procurement are now being integrated into the production and operational processes of PCB factories, fostering a more sustainable industry.
The process flow of PCBA (Printed Circuit Board Assembly) manufacturing is intricate and involves several crucial steps, such as PCB fabrication, component sourcing and inspection, SMT assembly, DIP insertion, and PCBA testing. Among these stages, PCBA testing is the most critical quality control phase, as it determines the final functionality and reliability of the product. So, what are the primary PCBA test methods?
PCBA testing encompasses five main types: ICT (In-Circuit Test), FCT (Functional Test), aging test, fatigue test, and testing under harsh environmental conditions. Here is an overview of each:
1. **ICT Test**
The ICT test primarily focuses on electrical checks, including continuity testing, voltage and current measurement, fluctuation analysis, amplitude checks, and noise detection. This step ensures that there are no electrical faults such as short circuits or open circuits, which could affect the board’s performance.
2. **FCT Test**
FCT involves functional testing by firing the IC program and simulating the entire PCBA’s functionality. It identifies issues in both hardware and software. This test requires the use of production fixtures and test racks to emulate real-world operating conditions and confirm that the PCBA works as intended.
3. **Aging Test**
The aging test involves subjecting a sample of PCBA boards to extended, high-frequency operational stress. This process is designed to simulate long-term usage and observe any failures or performance degradation over time. The results help assess the product’s longevity and predict failure probabilities under normal operating conditions.
4. **Fatigue Test**
In the fatigue test, PCBA boards undergo repeated or cyclic stress to simulate the wear and tear that can occur during normal operation. The goal is to evaluate the durability of the PCBA components over an extended period, identifying any potential weaknesses that may cause failures under prolonged usage.
5. **Harsh Environment Test**
This test exposes PCBA boards to extreme conditions such as high or low temperatures, high humidity, drops, splashes, and vibrations. By evaluating random samples under these stressful conditions, this test provides insights into the overall reliability and robustness of the entire batch of PCBA boards, predicting how the product will perform in demanding environments.
In conclusion, these five PCBA testing methods are essential for ensuring the quality and reliability of the final product. Each method serves a specific purpose, collectively providing a comprehensive assessment of the PCBA’s performance in both normal and extreme conditions.
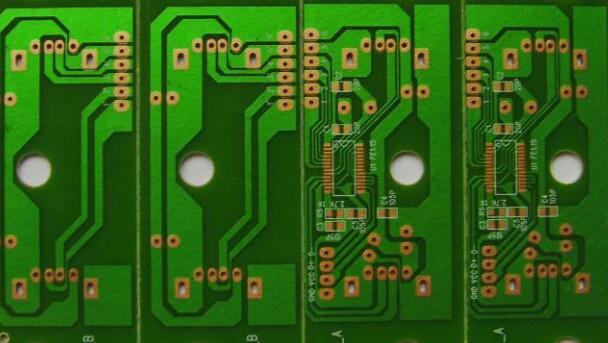
The aging test is primarily conducted by continuously powering the PCBA board and electronic products for an extended period. This process ensures that the products remain operational, allowing any potential failures or issues to be observed. After the aging test is completed successfully, the electronic products are considered ready for mass production and sale.
In this article, I will introduce the various PCBA testing methods. The PCBA manufacturing process is intricate, and during production, various issues can arise due to improper equipment or operational errors. As a result, there is no guarantee that all products will meet the required quality standards. To ensure that each product is free of defects, PCB testing is essential.
As environmental protection standards continue to rise and regulations become more stringent, PCB manufacturers face both challenges and opportunities. If these manufacturers can successfully address environmental concerns, particularly pollution, they will position themselves at the forefront of the market. This creates potential for growth and further development in the industry, especially for FPC (flexible printed circuit) products.
The rise of the internet has significantly transformed traditional marketing methods. By leveraging the internet, resources are consolidated on a larger scale, accelerating the development of FPC flexible circuit boards. As development accelerates, PCB manufacturers must also address the environmental challenges that arise from this rapid expansion. However, the internet’s growth has also brought significant advancements in environmental protection and information technology. Data centers dedicated to environmental monitoring and the concept of green electronics procurement are now being integrated into the production and operational processes of PCB factories, fostering a more sustainable industry.