1 PCB prototype boards are essentially early samples of products, with the main purpose of testing the functionality of design concepts.
2 Designers and engineers use different types of PCB prototypes to test various aspects of the selected design.
3 Although most prototypes are only made to test basic user functionality, PCB prototype boards still need to be functional to some extent, as PCB prototyping is made to test the overall functionality of the design.

During the PCB prototype board production process, engineers can conduct experiments on different PCB designs and manufacturing specifications to find the most effective one.
Advantages of PCB prototype board
1. Shorten time and save costs
In the process of designing a PCB, engineers perform multiple iterations before creating the final product, which can result in a lengthy timeline. However, PCB prototype boards can help accelerate the entire design and manufacturing process by:
1) Complete testing
PCB prototype boards can help PCB design engineers quickly and accurately test design problems. Without this point, discovering design defects would take more time, and if not delivered promptly, it may lead to customer dissatisfaction and result in a loss of revenue.
2) Customers see the product in advance for better communication
Customers usually hope to see the product at multiple points during the production process and provide prototypes as assistance, which can help better conduct the design. It can also minimize communication with customers and the time they require for a redesign.
3) Minimize rework to the greatest extent possible
PCB prototype board testing allows for the inspection and testing of circuit boards before production, reducing rework. If a defective product is put into production, it will take longer and cost more in the later stage.
2. Being able to detect defects as soon as possible
Prototyping design can catch design defects in the early stages of the product development process, and make factory changes in the early stages of the process to avoid a series of potential issues that may affect various aspects of the project.
3. Ability to test components separately
It is very useful to test different components separately for complex PCB-based project components. By individually verifying each component, any issues that may occur can be identified.
4. Reduce costs
PCB prototype versions can reduce the total cost of projects, identify problems faster, and fix them before mass production runs.
5. Improve the final product
PCB prototype board design helps to improve each PCB and component, thereby achieving a higher quality design.
Type of prototype board
1. Solderless Breadboard
The solderless Breadboard allows all electronic components to be assembled in the design concept and connected by jumpers. There are no welded connections in this prototype board. Therefore, changing, adding, or removing any electronic components becomes simple and fast. In addition, due to the reduced time required to assemble components, it allows for rapid testing.
Breadboard has some matrix-shaped small holes for assembling components. These holes have a metal coating that allows for conduction. These Breadboard are made of plastic, and some Breadboard may also be made of wood.
2. Soldered protoboard
The soldered Breadboard, also known as the welded prototype board, is similar to the solderless Breadboard in appearance and appearance. However, this can withstand welding. This means that people can assemble electronic components and weld them to achieve Tight junctions. These are usually made of wood or silicon instead of plastic.
3. Wire wrap boards
The winding board requires welding of the components. The upper surface has all components welded and connected using wires from the lower surface. These are similar to welded Breadboards but provide better reliability. Therefore, novice enthusiasts can safely test their design ideas using a winding board. However, metal wire packaging boards are not very popular and have limited supply in most retail markets.
4. Etching circuit boards
These are the most difficult to use. The use of etching circuit boards requires printing the PCB and etching it onto a hard surface (circuit board) made of wood, silicon, etc. In addition, these circuit boards also need to be etched with special chemicals to form an insulation coating on the top to protect the circuit board. Therefore, etching circuit boards is only suitable for advanced users.
On a PCB prototype board, people can assemble all electronic components, connect them, and test the initial prototype for errors and functionality. Once the prototype or sample passes all validity and validation tests, the product is marked as suitable for mass production and safe use. PCB prototype boards are used to test whether product design concepts may be suitable for use.
2 Designers and engineers use different types of PCB prototypes to test various aspects of the selected design.
3 Although most prototypes are only made to test basic user functionality, PCB prototype boards still need to be functional to some extent, as PCB prototyping is made to test the overall functionality of the design.
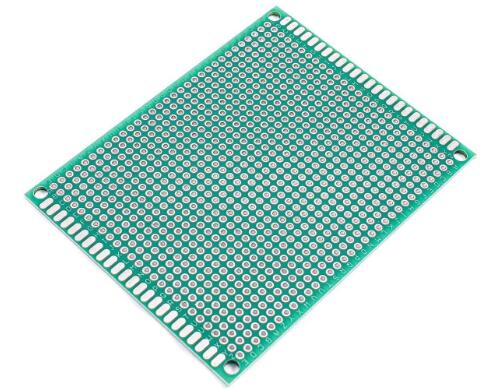
During the PCB prototype board production process, engineers can conduct experiments on different PCB designs and manufacturing specifications to find the most effective one.
Advantages of PCB prototype board
1. Shorten time and save costs
In the process of designing a PCB, engineers perform multiple iterations before creating the final product, which can result in a lengthy timeline. However, PCB prototype boards can help accelerate the entire design and manufacturing process by:
1) Complete testing
PCB prototype boards can help PCB design engineers quickly and accurately test design problems. Without this point, discovering design defects would take more time, and if not delivered promptly, it may lead to customer dissatisfaction and result in a loss of revenue.
2) Customers see the product in advance for better communication
Customers usually hope to see the product at multiple points during the production process and provide prototypes as assistance, which can help better conduct the design. It can also minimize communication with customers and the time they require for a redesign.
3) Minimize rework to the greatest extent possible
PCB prototype board testing allows for the inspection and testing of circuit boards before production, reducing rework. If a defective product is put into production, it will take longer and cost more in the later stage.
2. Being able to detect defects as soon as possible
Prototyping design can catch design defects in the early stages of the product development process, and make factory changes in the early stages of the process to avoid a series of potential issues that may affect various aspects of the project.
3. Ability to test components separately
It is very useful to test different components separately for complex PCB-based project components. By individually verifying each component, any issues that may occur can be identified.
4. Reduce costs
PCB prototype versions can reduce the total cost of projects, identify problems faster, and fix them before mass production runs.
5. Improve the final product
PCB prototype board design helps to improve each PCB and component, thereby achieving a higher quality design.
Type of prototype board
1. Solderless Breadboard
The solderless Breadboard allows all electronic components to be assembled in the design concept and connected by jumpers. There are no welded connections in this prototype board. Therefore, changing, adding, or removing any electronic components becomes simple and fast. In addition, due to the reduced time required to assemble components, it allows for rapid testing.
Breadboard has some matrix-shaped small holes for assembling components. These holes have a metal coating that allows for conduction. These Breadboard are made of plastic, and some Breadboard may also be made of wood.
2. Soldered protoboard
The soldered Breadboard, also known as the welded prototype board, is similar to the solderless Breadboard in appearance and appearance. However, this can withstand welding. This means that people can assemble electronic components and weld them to achieve Tight junctions. These are usually made of wood or silicon instead of plastic.
3. Wire wrap boards
The winding board requires welding of the components. The upper surface has all components welded and connected using wires from the lower surface. These are similar to welded Breadboards but provide better reliability. Therefore, novice enthusiasts can safely test their design ideas using a winding board. However, metal wire packaging boards are not very popular and have limited supply in most retail markets.
4. Etching circuit boards
These are the most difficult to use. The use of etching circuit boards requires printing the PCB and etching it onto a hard surface (circuit board) made of wood, silicon, etc. In addition, these circuit boards also need to be etched with special chemicals to form an insulation coating on the top to protect the circuit board. Therefore, etching circuit boards is only suitable for advanced users.
On a PCB prototype board, people can assemble all electronic components, connect them, and test the initial prototype for errors and functionality. Once the prototype or sample passes all validity and validation tests, the product is marked as suitable for mass production and safe use. PCB prototype boards are used to test whether product design concepts may be suitable for use.